In France, at the gates of Paris, the Sèvres Manufacture is committed to transmitting a know-how that is more than three centuries old! Since the creation of this porcelain factory under Louis XV in 1740, Sèvres has built up a reputation commensurate with its talent. Each piece that leaves its workshops, from the smallest saucer to the most imposing vase, is a masterpiece that makes its craftsmen proud.
But can you still be modern when you have blown out your 280th candle? Today, Sèvres collaborates with the greatest contemporary artists to create remarkable pieces, pushing the technical limits even further without turning its back on its rich history. Let’s discover this factory – a little bit magical – that manages to transform pebbles into ultra-luxury!
Summary
A short history of Sèvres Porcelain
Born in China, porcelain fascinates by its whiteness and translucency. Under the Ancien Régime, it was nicknamed “white gold”: it was an ultra-luxury item, extremely sought after, so much so that several European courts set out to discover the secrets of its manufacture. Knowing how to make porcelain then became a real political issue!
What is porcelain?
Porcelain is a material composed of three rocks: kaolin, feldspar and quartz. Its whiteness is close to the mother-of-pearl of the shell “porcellana”, which gave it its name.
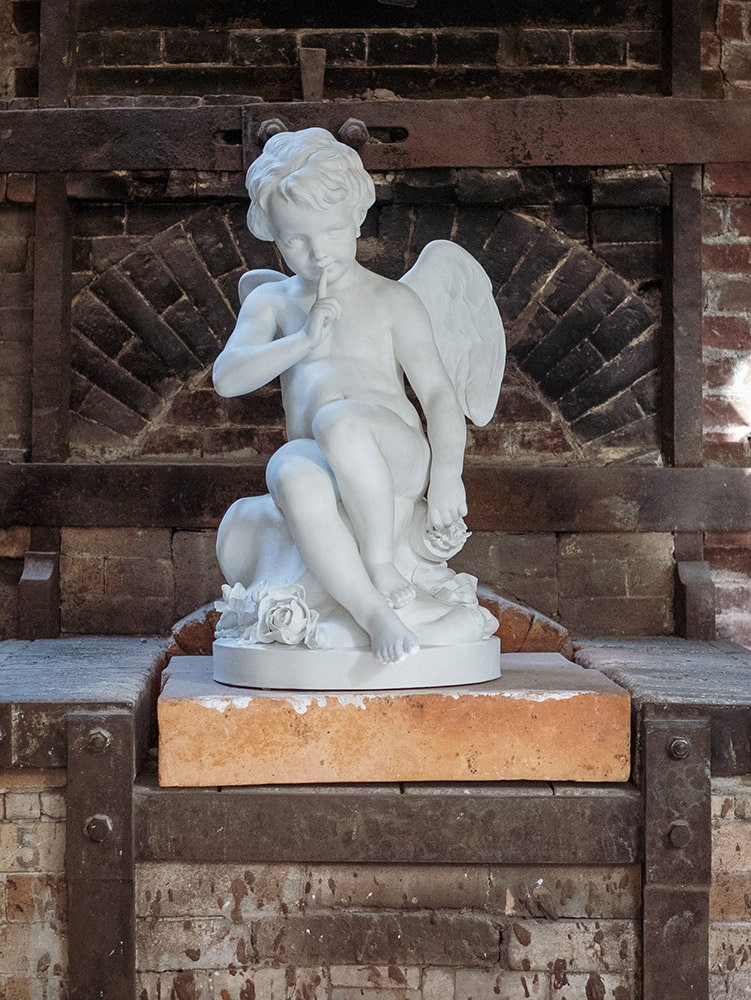
At the beginning of the 18th century, the discovery of a kaolin deposit in Saxony allowed the creation of the first porcelain factory outside of China, the royal factory in Meissen. France then took on the challenge of unlocking the mysteries of its manufacture.
Father François-Xavier d’Entrecolles, a Jesuit from Limoges on a mission to China, described for the first time the technique of porcelain manufacture – this was one of the first cases of industrial espionage! At the same time, Louis XV, encouraged by Madame de Pompadour, financed the creation of the Manufacture de Vincennes in 1740, which managed to carry out conclusive tests. French creations became luxury products, able to compete with porcelain from China or Saxony.
In 1756, the factory was transferred to Sèvres under the impetus of Madame de Pompadour, who owned her castle of Bellevue not far away. That same year, Louis XV became the sole shareholder of the factory and attached it to the Crown’s domain in 1759. From then on, the factory remained attached to the power of the State (the Crown, the Empire or the Republic, according to the regimes) which made it possible to preserve its archives and its know-how.
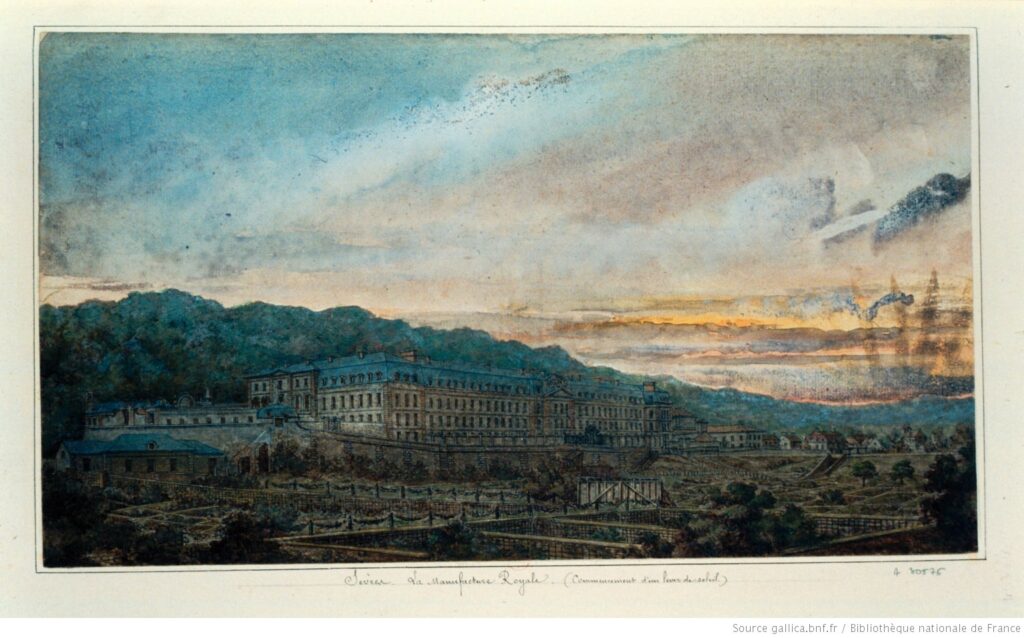
Visit of the Sèvres Manufacture
Pushing the doors of the Sèvres factory gives the impression of a timetravel because if the technological advances have facilitated on certain points the production methods, it has never been at the expense of the hand. Thus, the furnaces have evolved, the turning of certain pieces is done thanks to electricity … but almost all the tasks remain manual because porcelain is a capricious material that the machine can hardly tame. The Sèvres factory thus claims a niche production to create art objects in small series.
“We prefer to produce few, beautiful and perfect.”
The manufacture of a porcelain goes through several stages. For some pieces, the porcelain arrives in liquid form (known as barbotine) and is poured into one of the 100,000 plaster molds that the factory keeps in reserve, a treasure nicknamed “The Magot”!
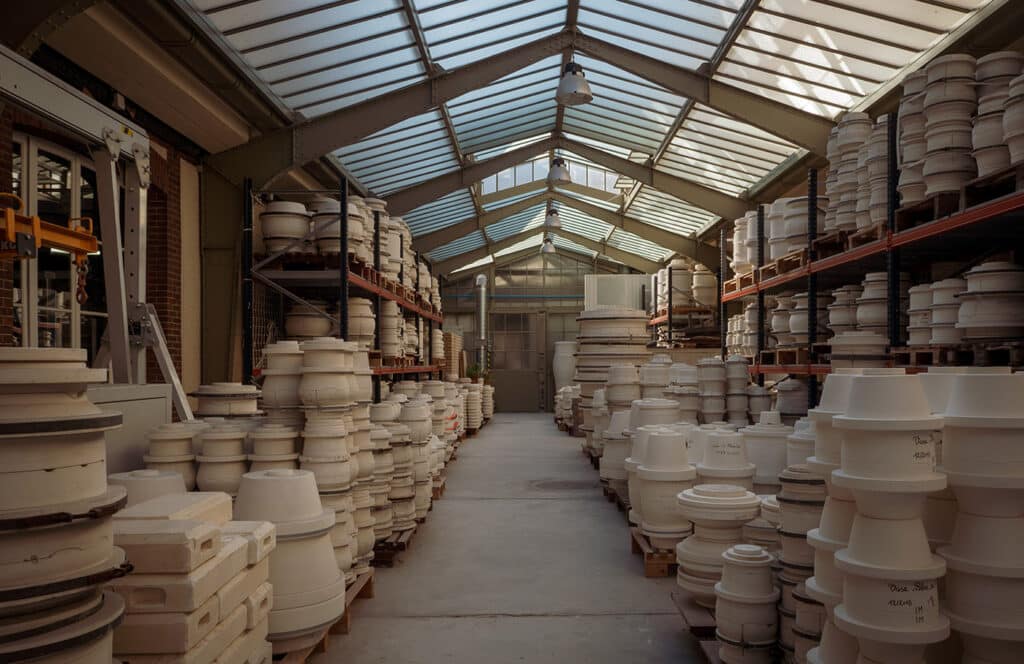
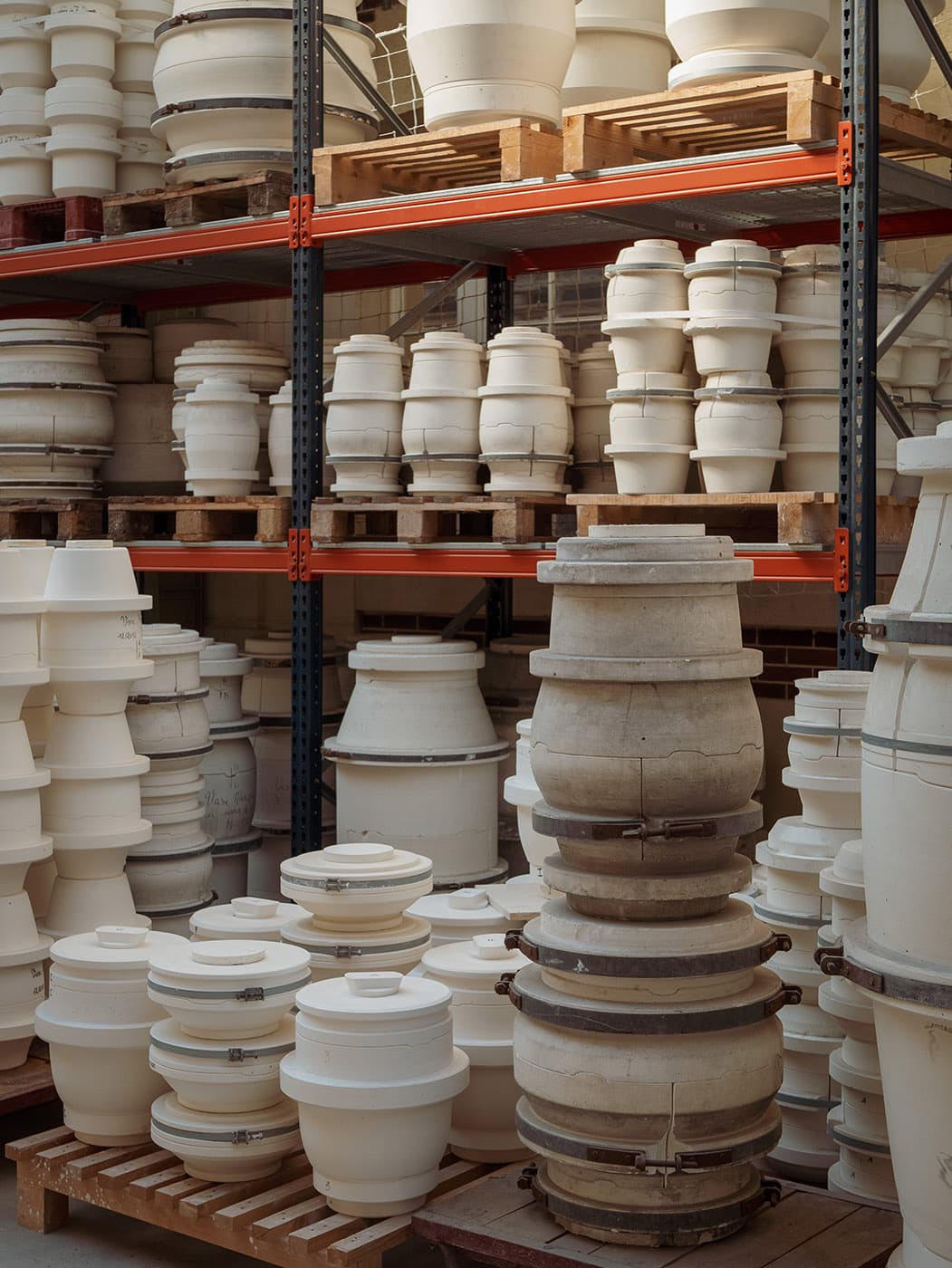
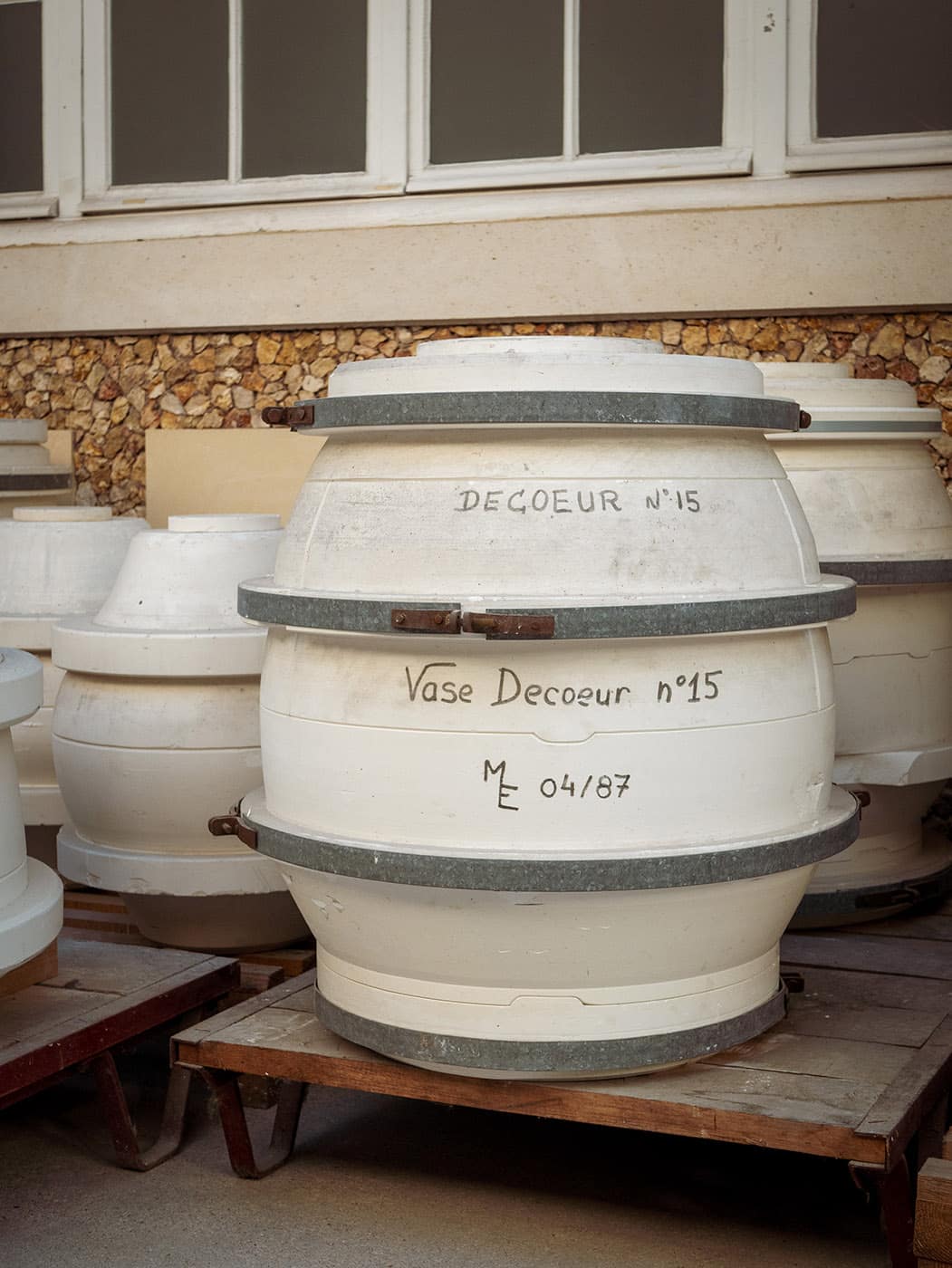
Once cast and after drying, the pieces are then meticulously retouched by hand.
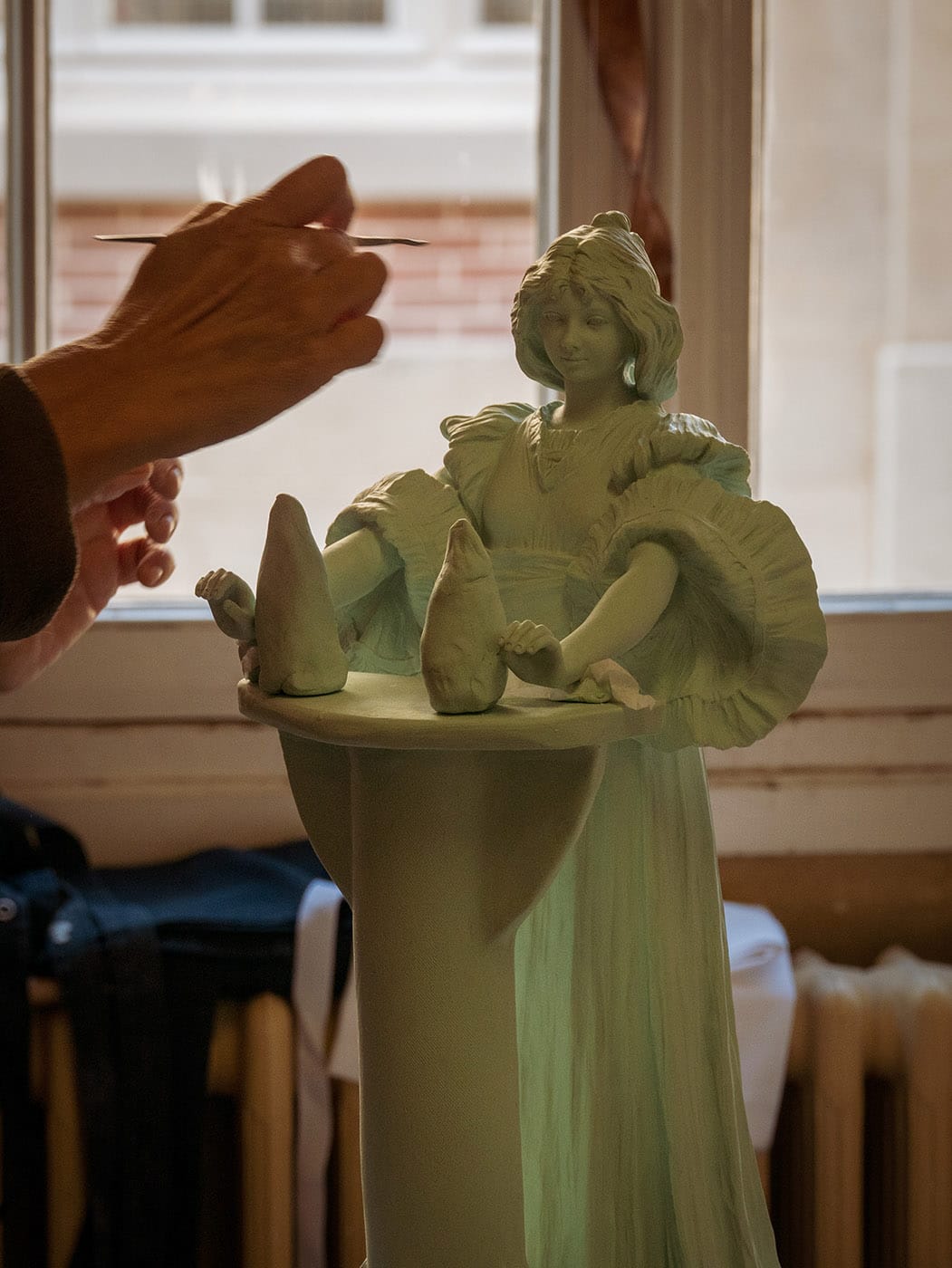
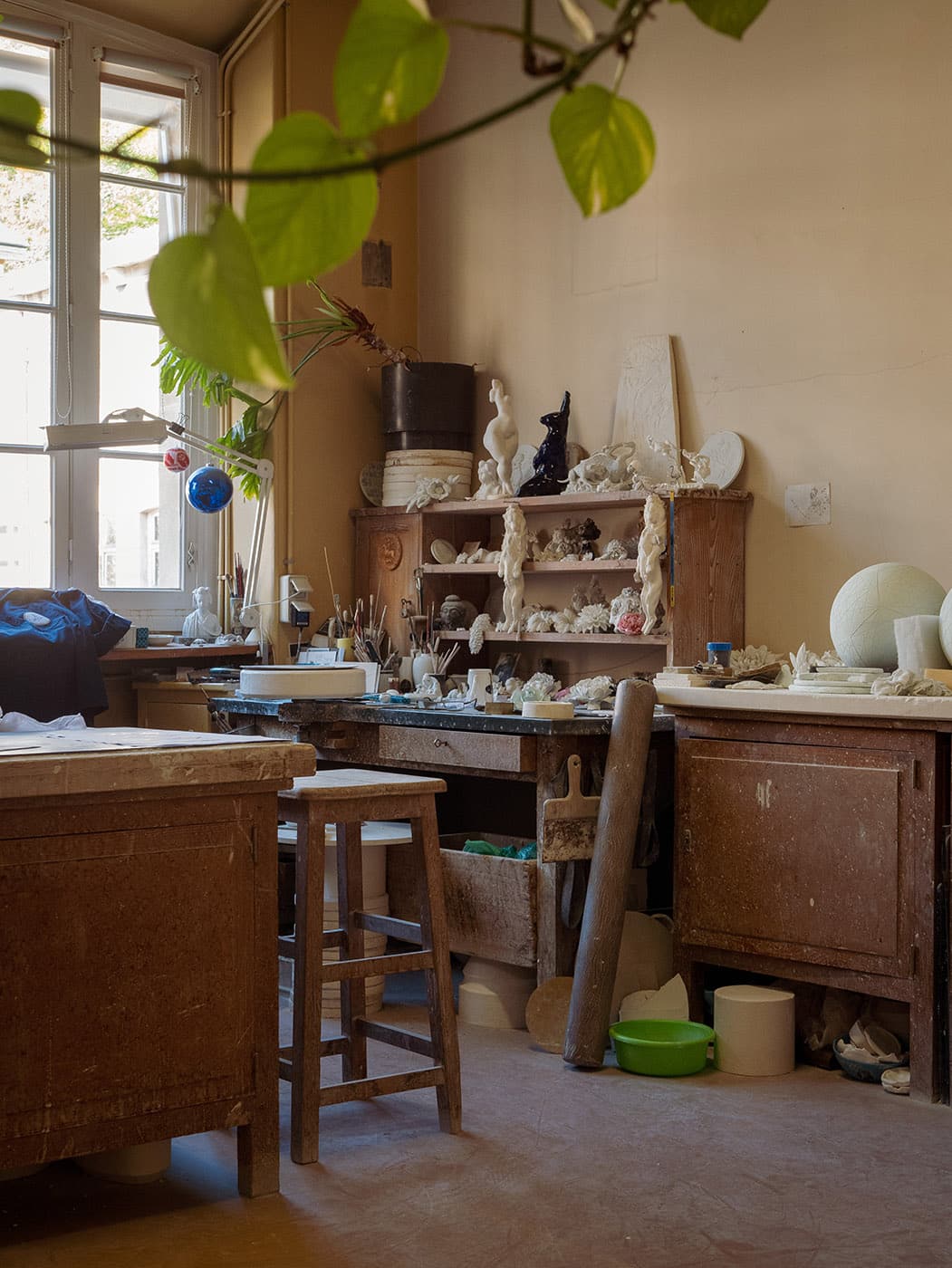
For other creations, soft paste porcelain is used in the sculpture or turning workshops.
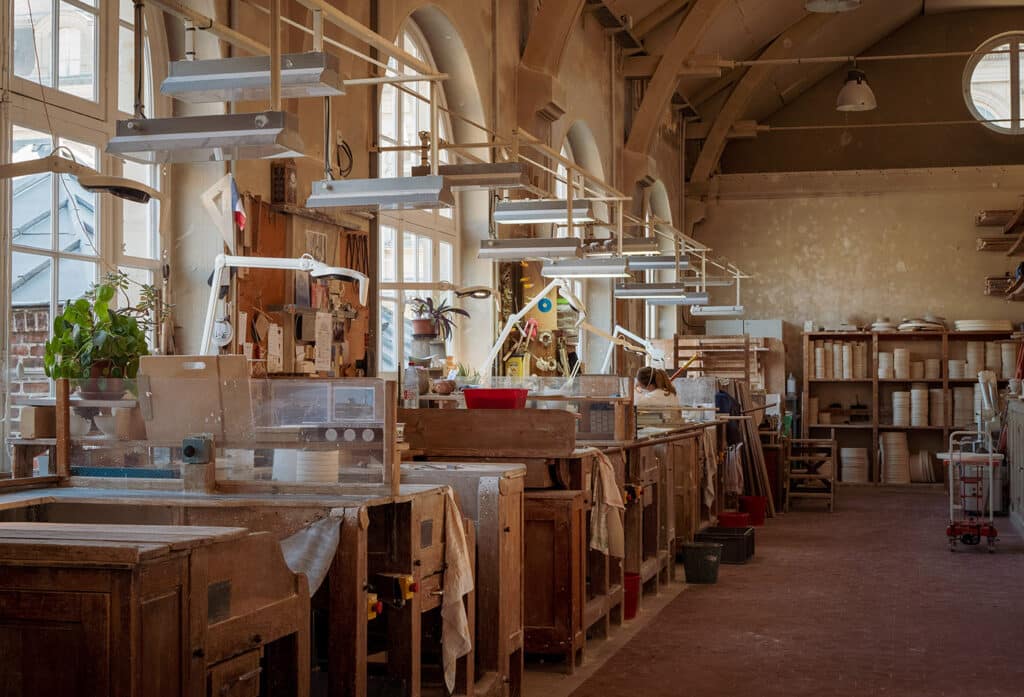
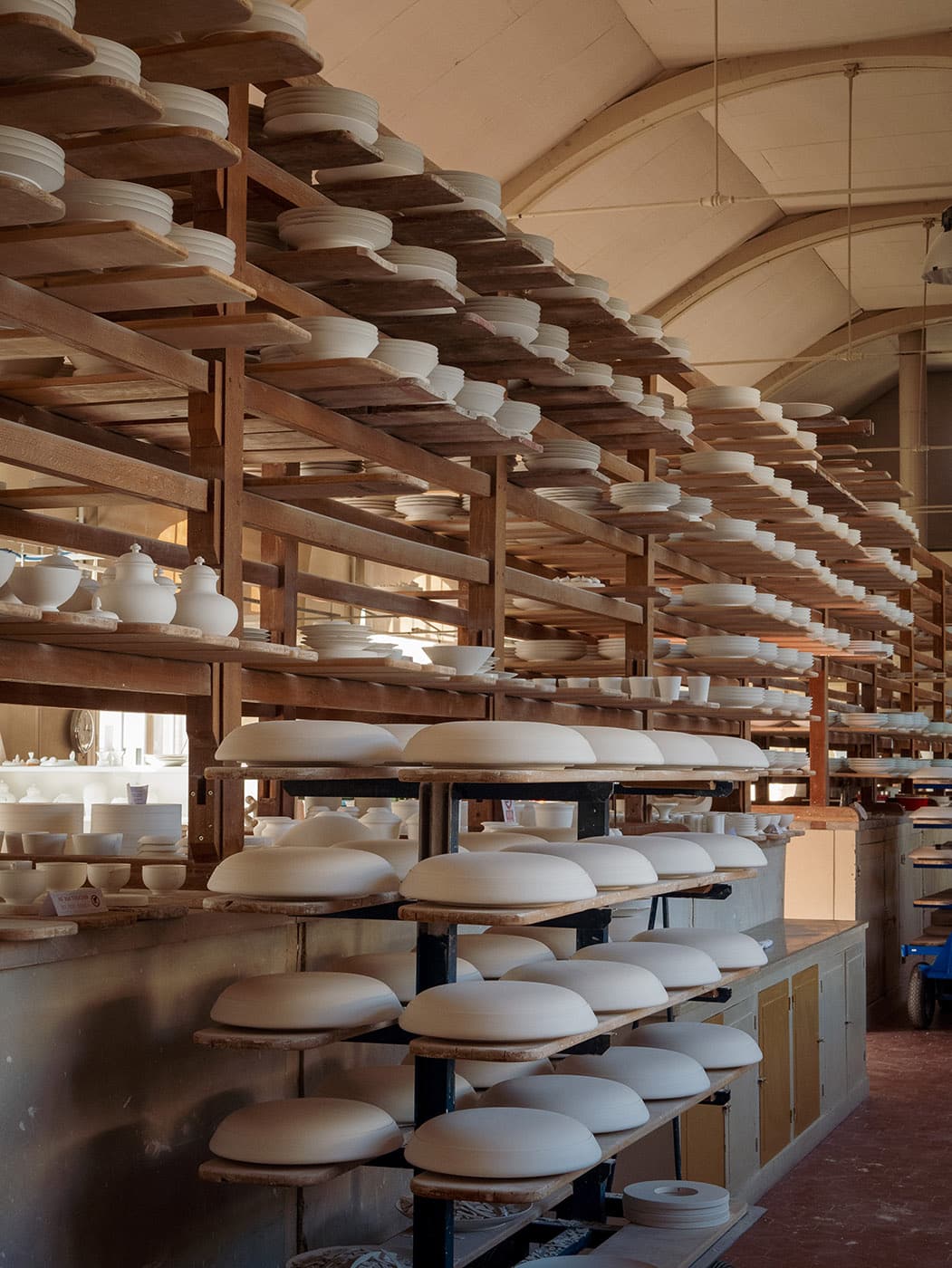
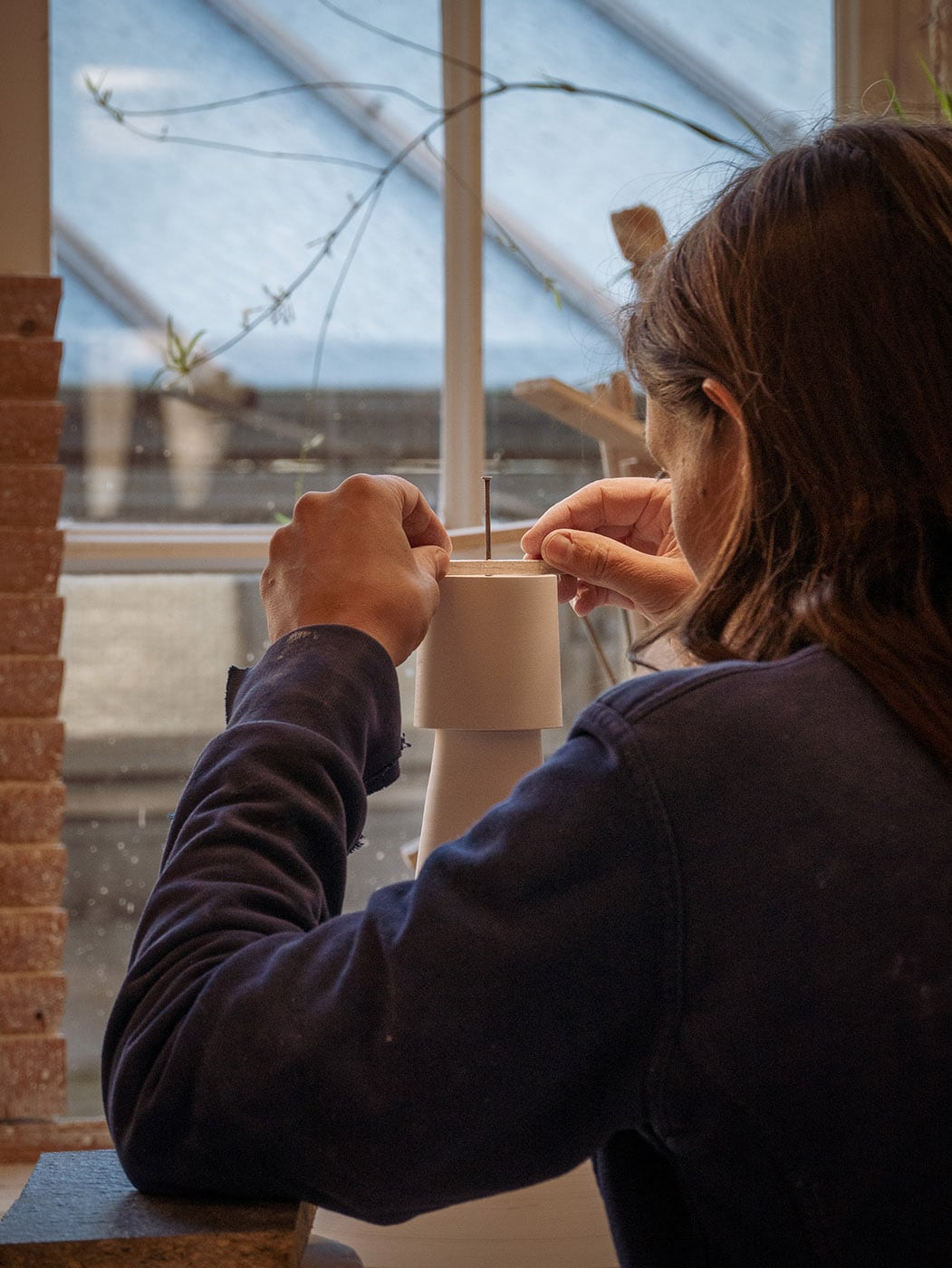
Do not lose the know-how
The factory has six wood-fired kilns, but only one is still in working order. This method of firing requires 33 hours to reach 1200 degrees; the supply of 4 furnaces continuously and then a month of rest before opening to avoid thermal shock – which makes it a particularly laborious tool.
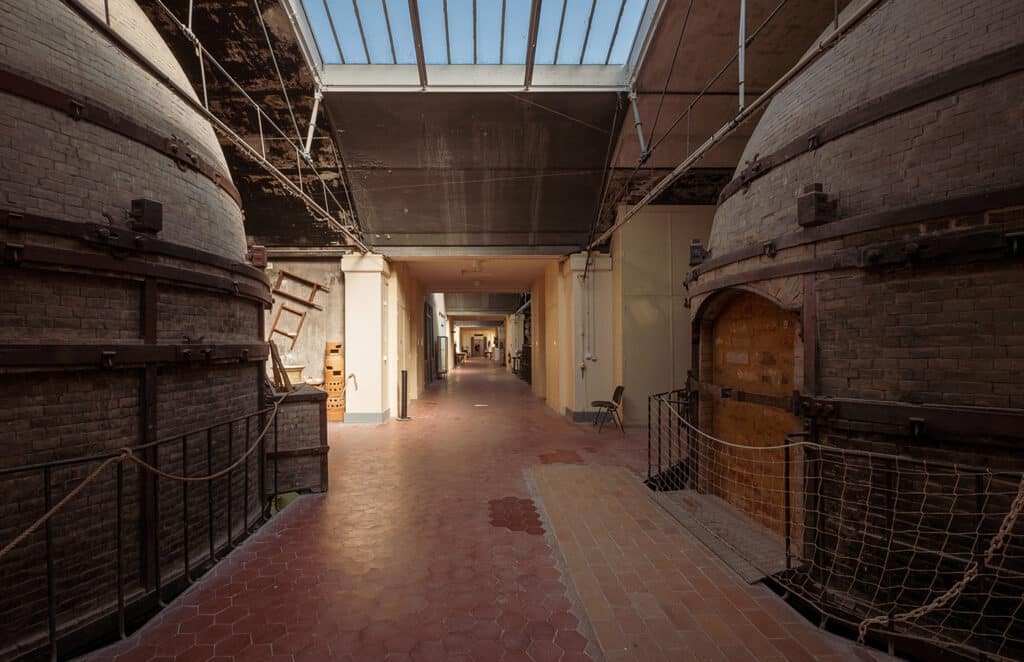
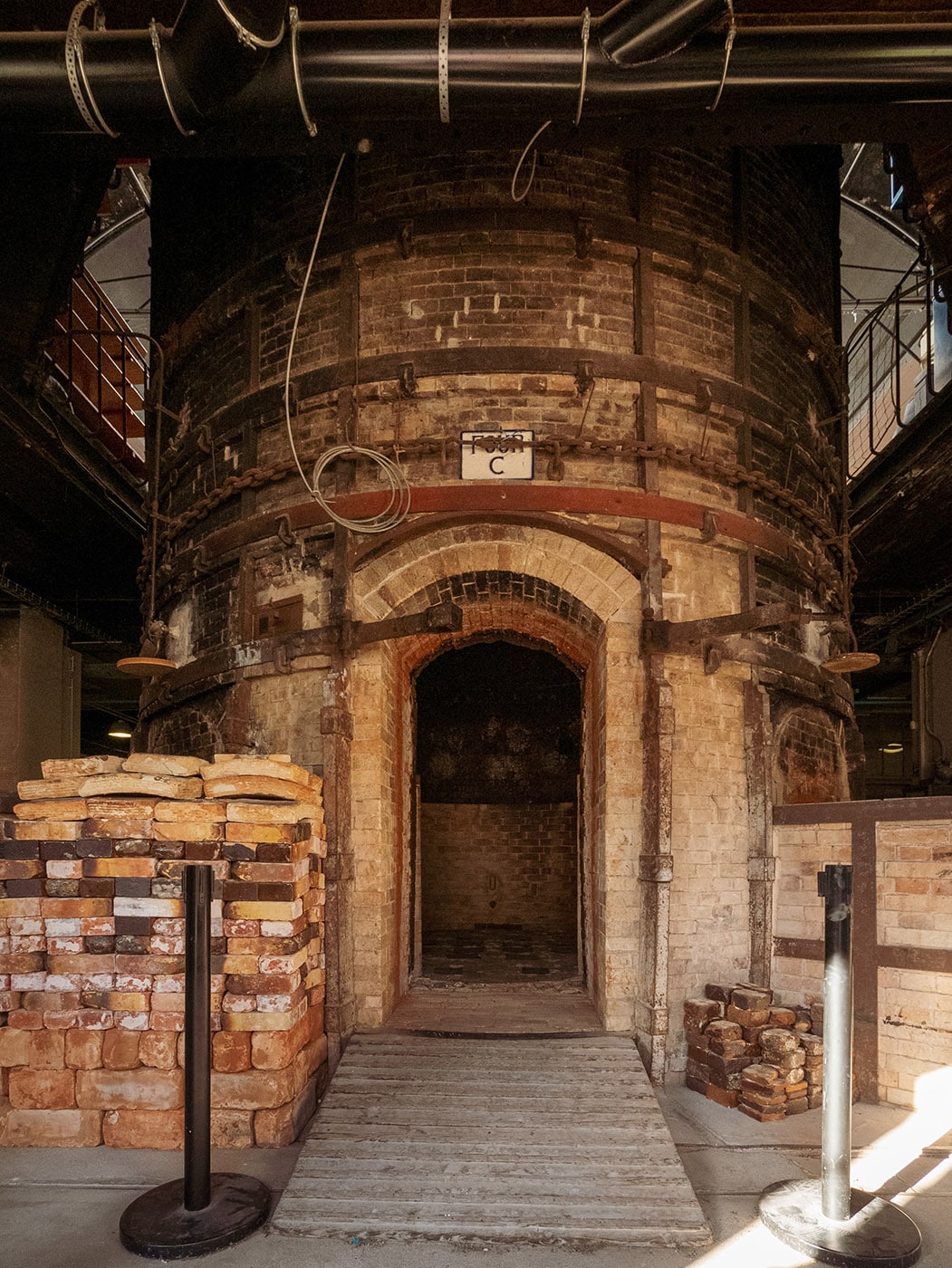
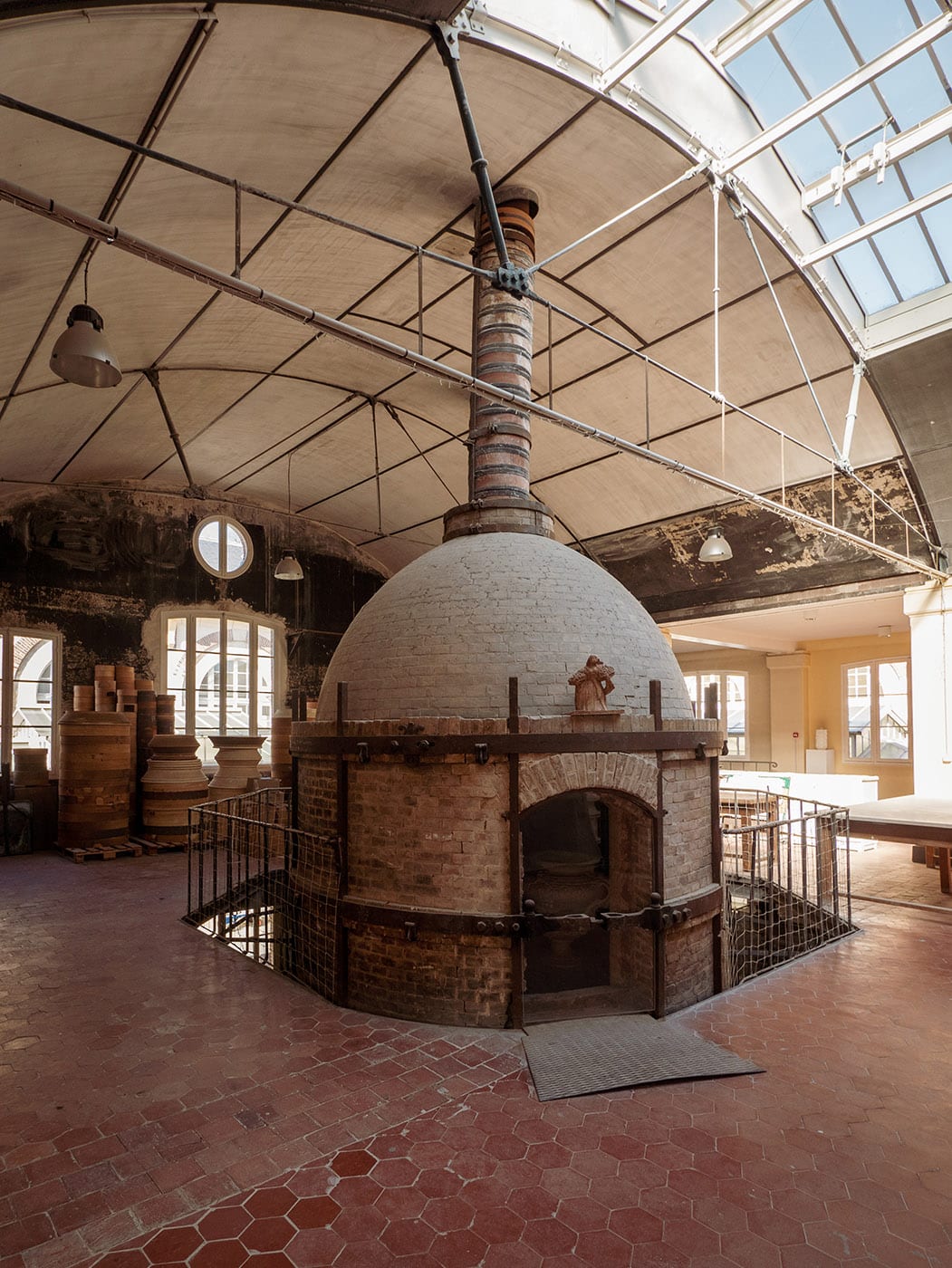
Although new, more modern ovens are used today, the wood-fired oven is still put into service every four years to ensure that this know-how is not lost and is passed on.
Among the various workshops at Sèvre, one of the most impressive is the one dedicated to painting. Here, the craftsmen work blindly because the colors change during the firing process. They must therefore use a “palette” developed during their apprenticeship as a reference. A distinction is made between high fire and low fire colors, which fire above and below 1000 degrees respectively. Most pieces require several attempts at painting before the final version is validated. Some designs require up to 300 hours of work! It can take up to 6 years to produce a batch of 12 plates for the most complex designs.
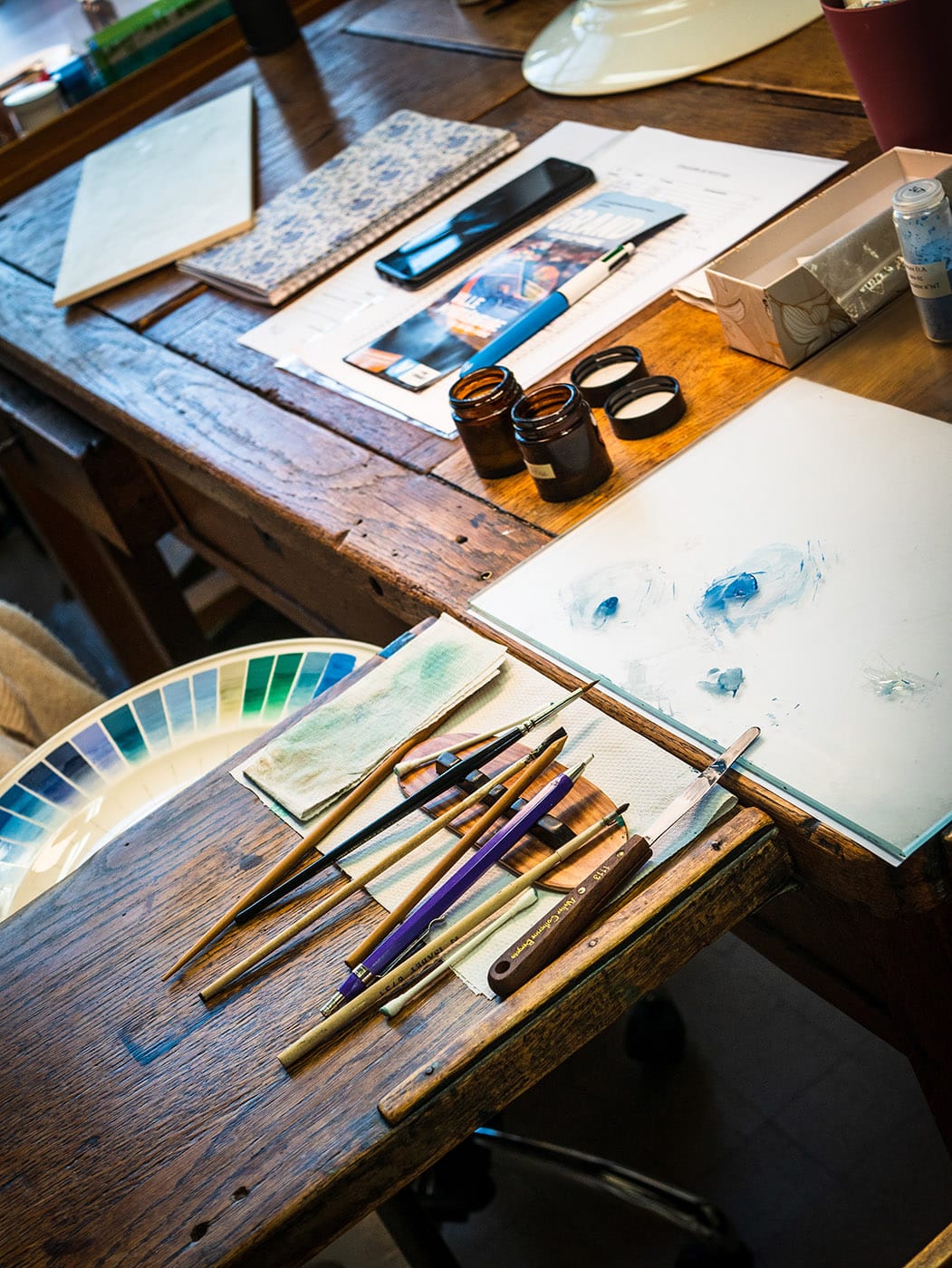
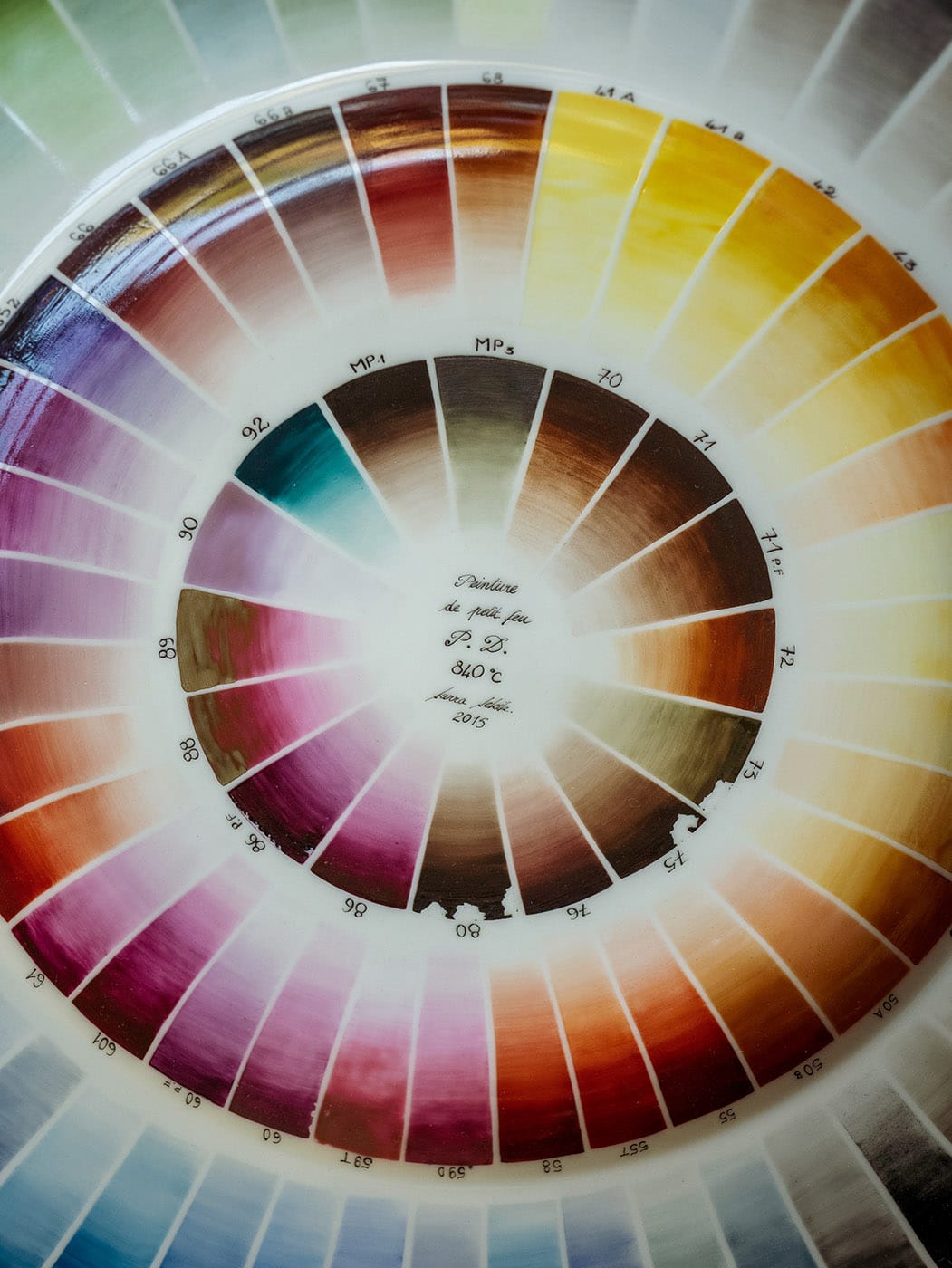
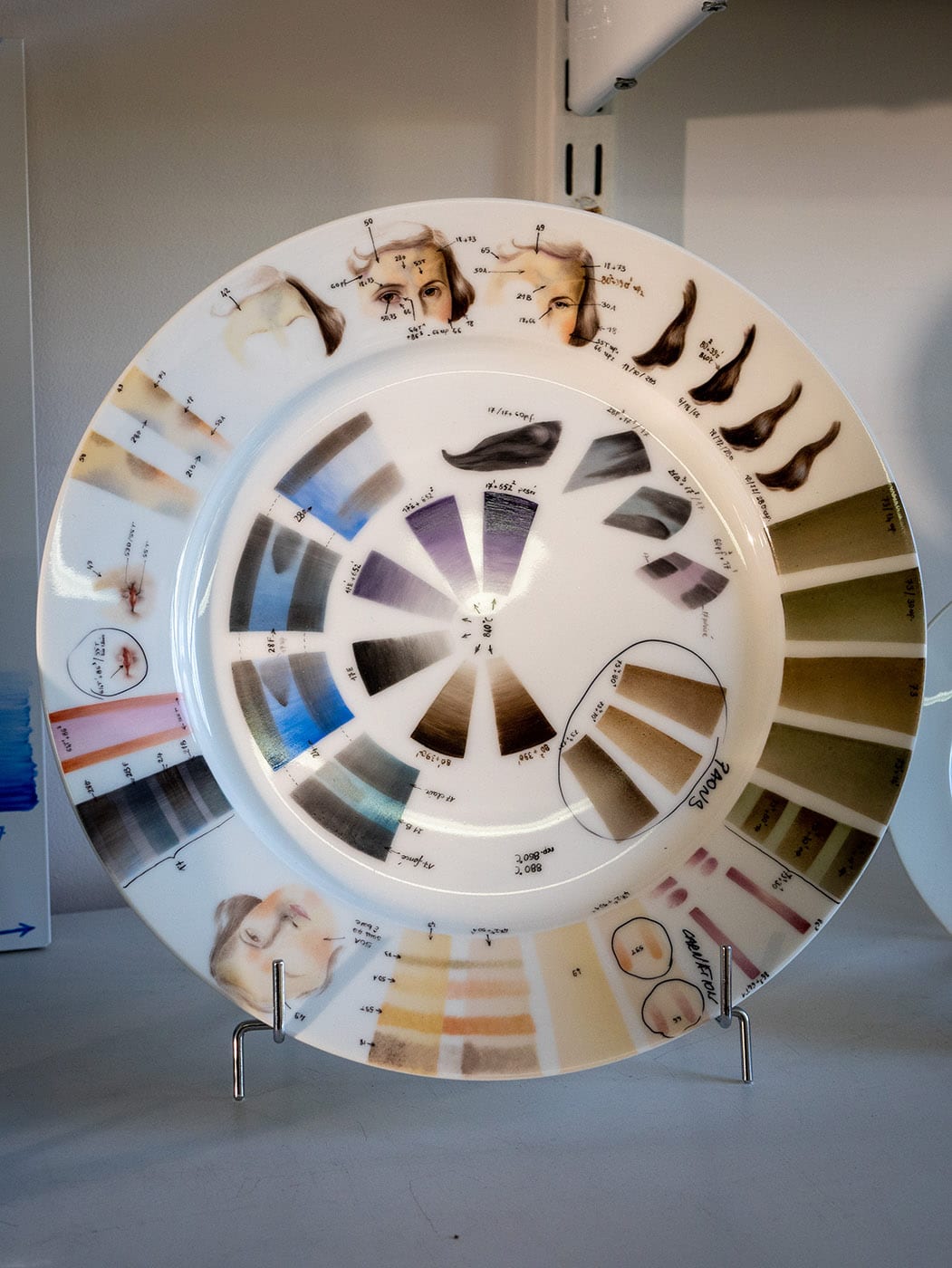
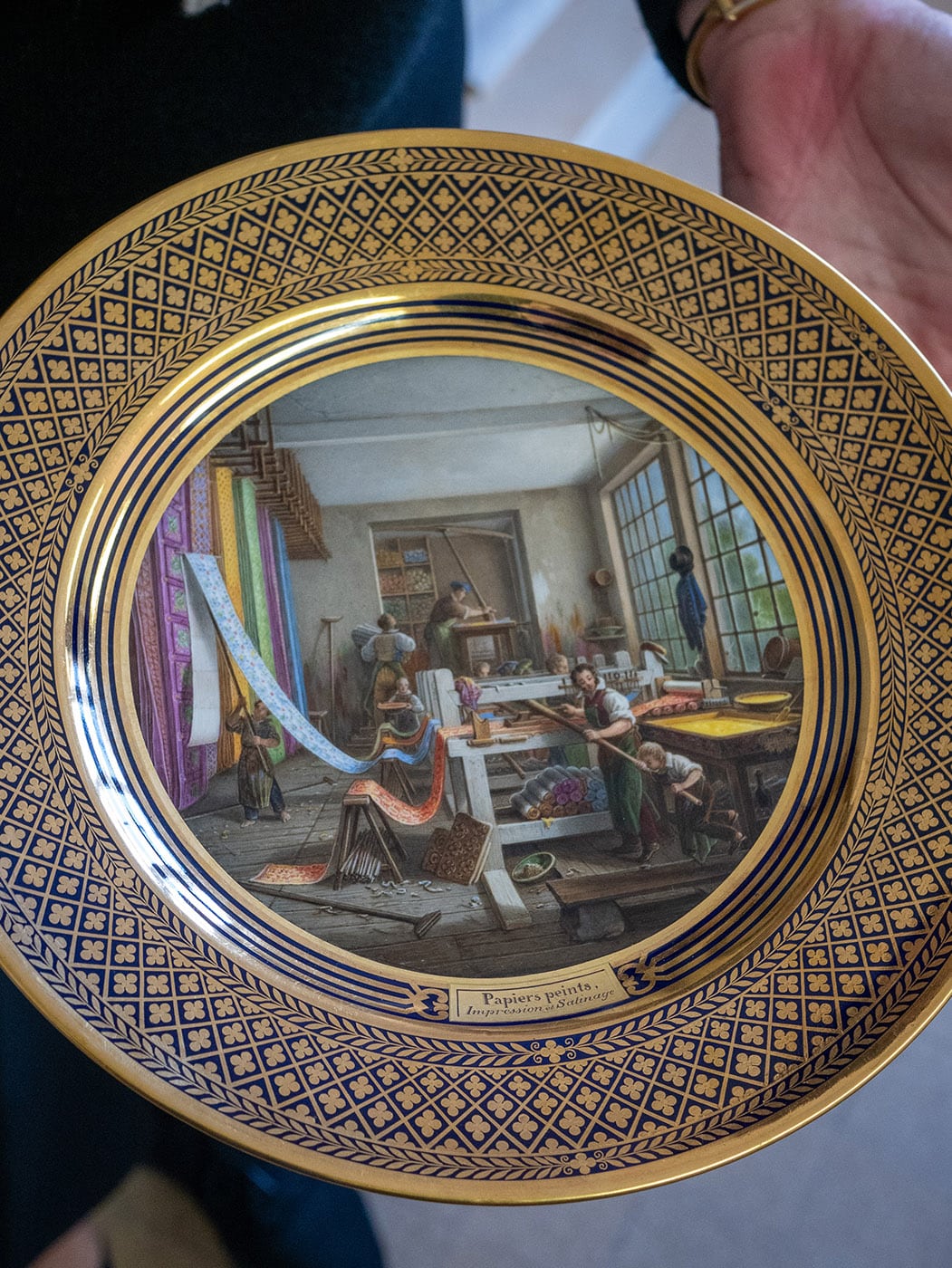
The Sèvres palette now includes more than 1000 colors, including the famous “Sèvres blue” which has become the identity of the factory! This last one requires three successive poses (and thus three firings) to give it this intensity.
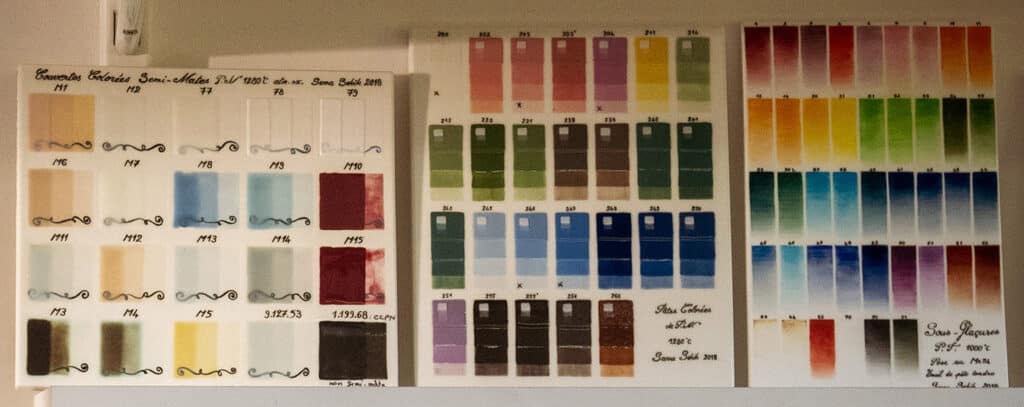
Most of the pieces produced at Sèvre, especially those related to the art of the table (cups, plates…) then go to the spinning-gold workshop. Crushed gold mixed with essential oil of lavender is applied by hand.
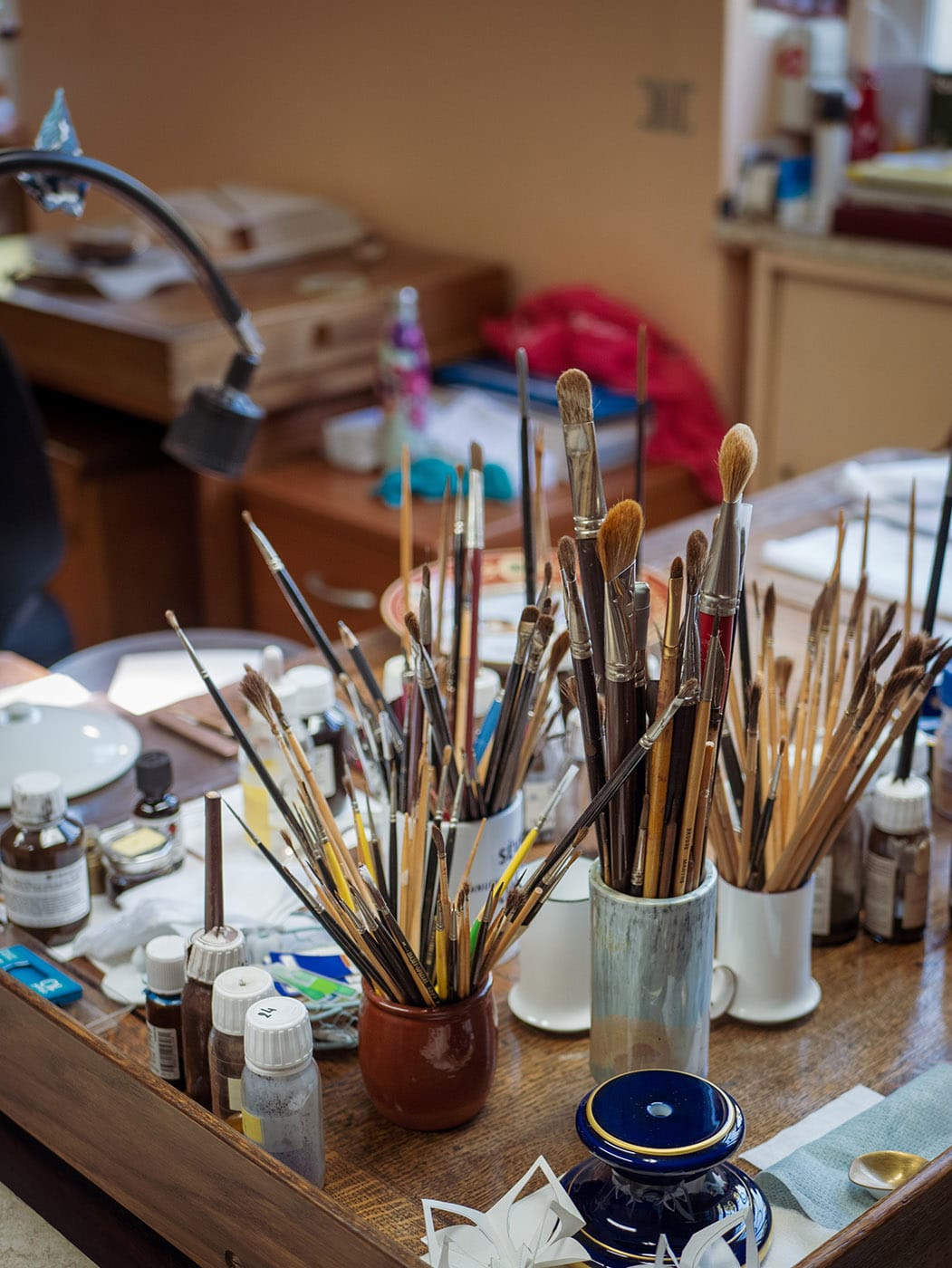
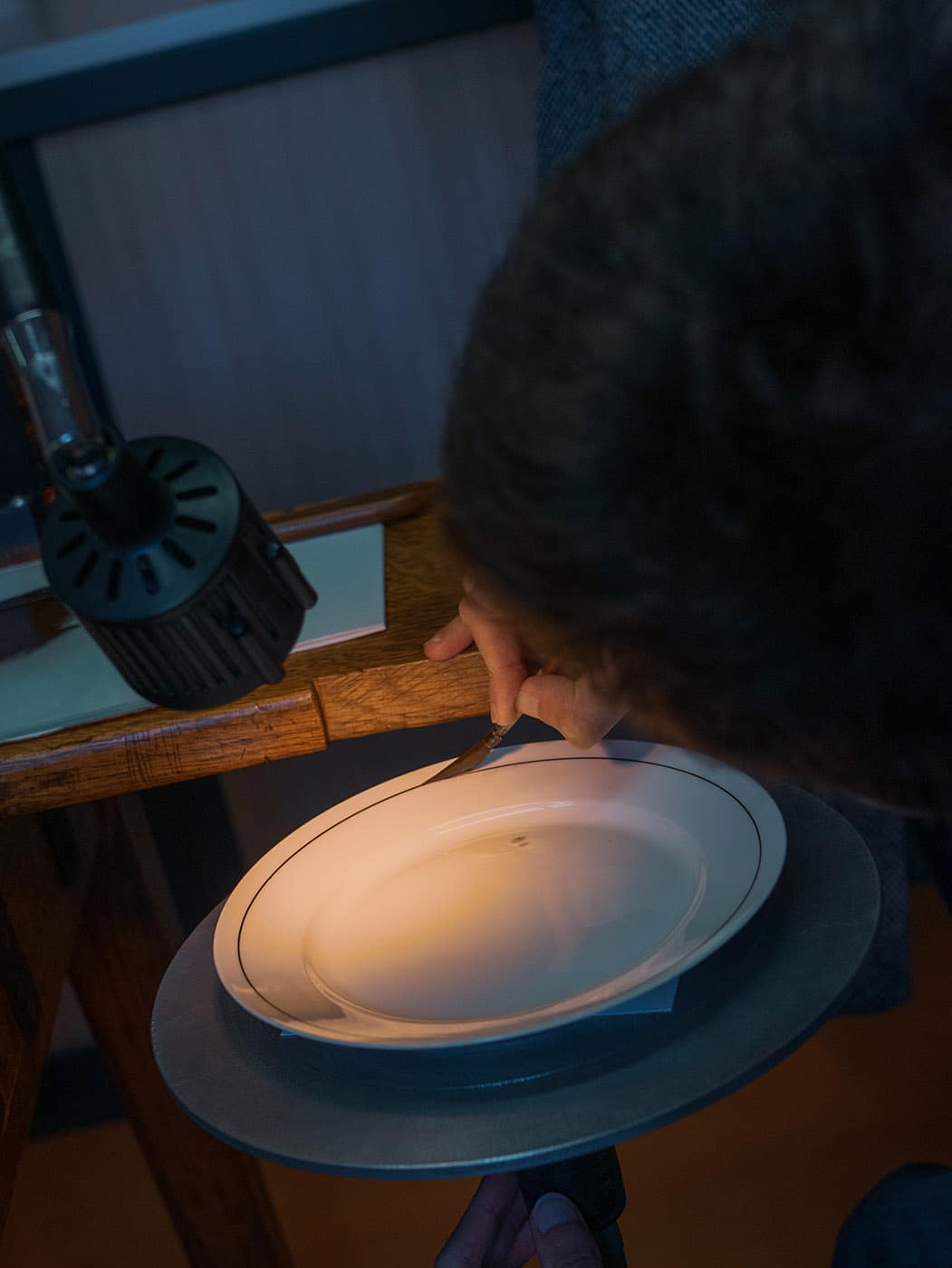
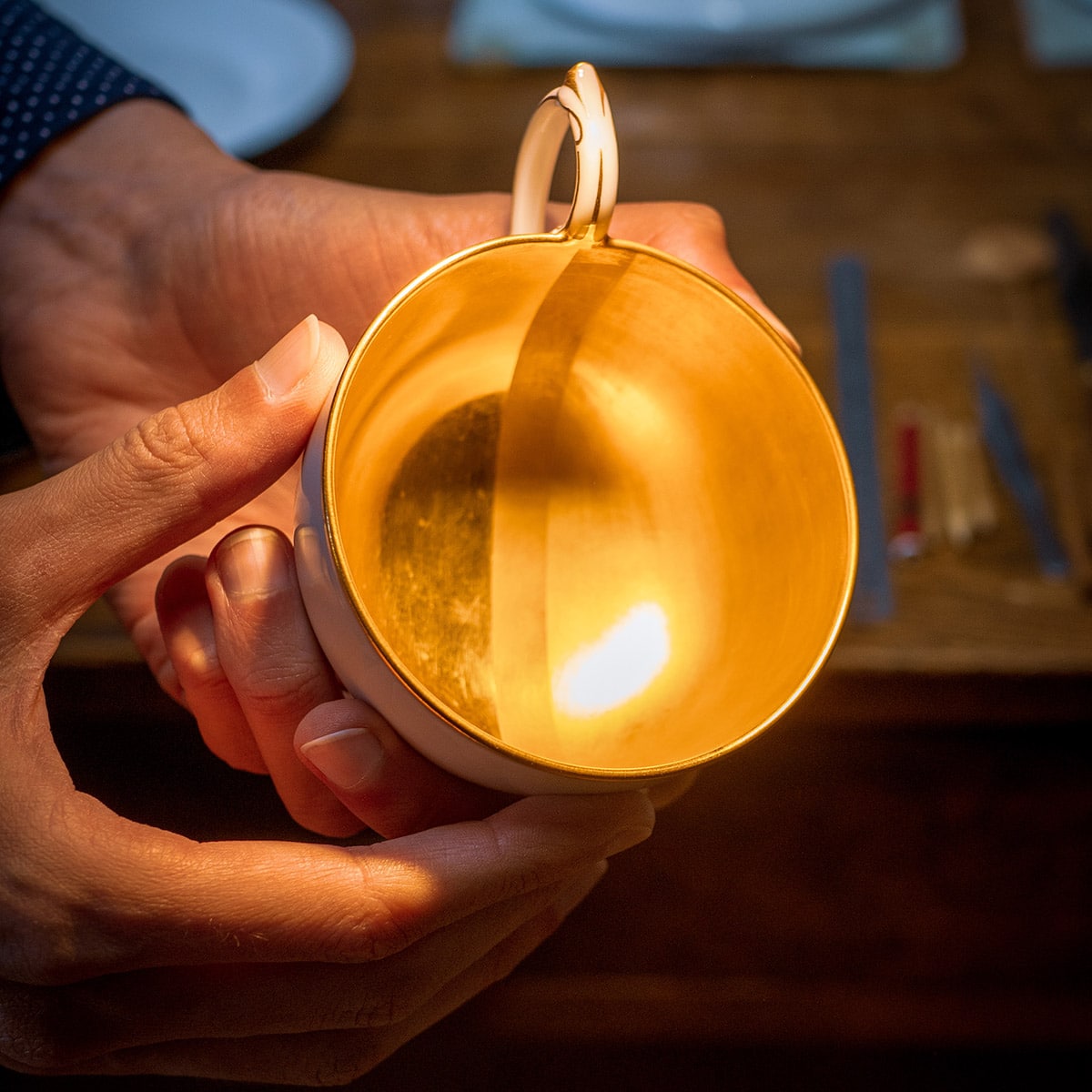
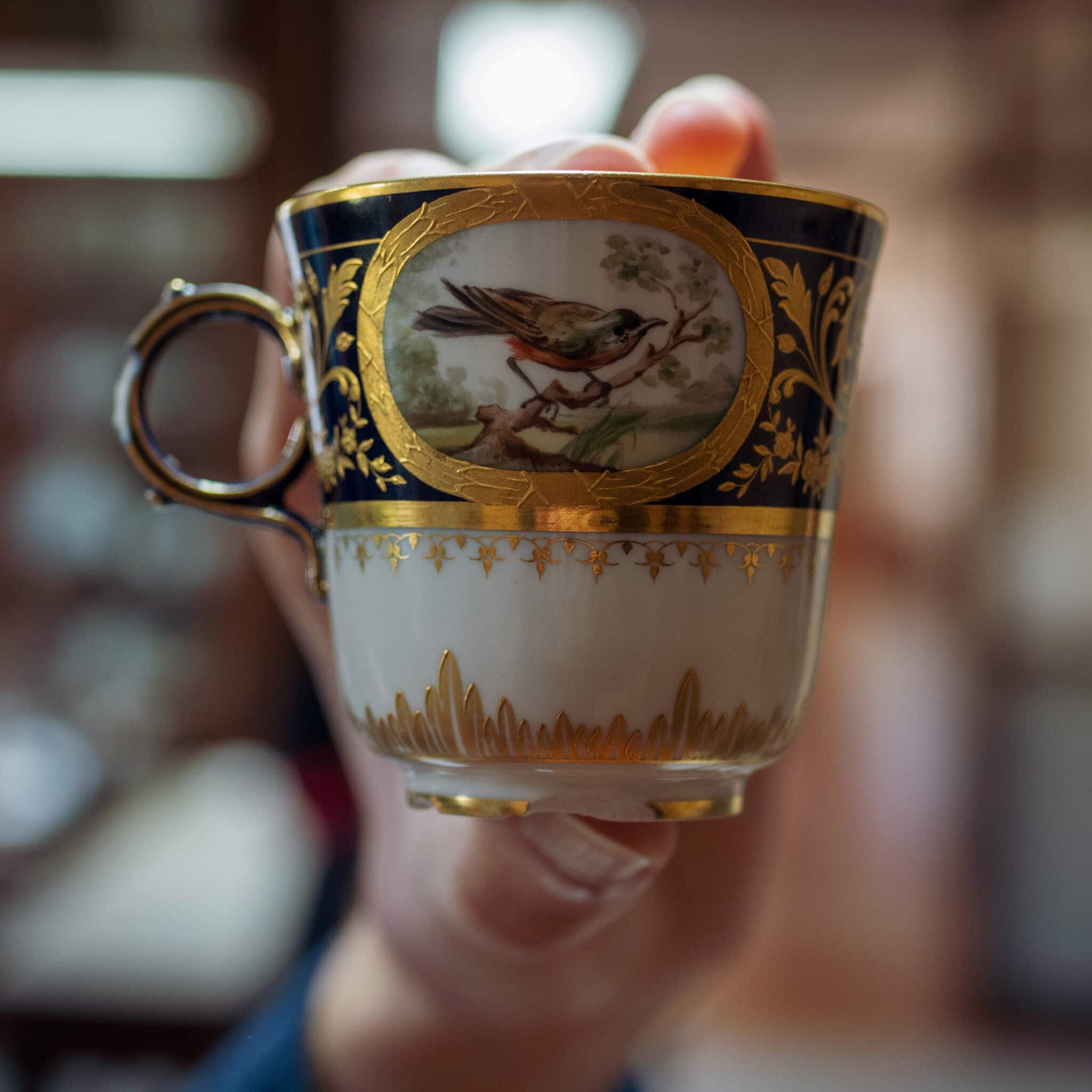
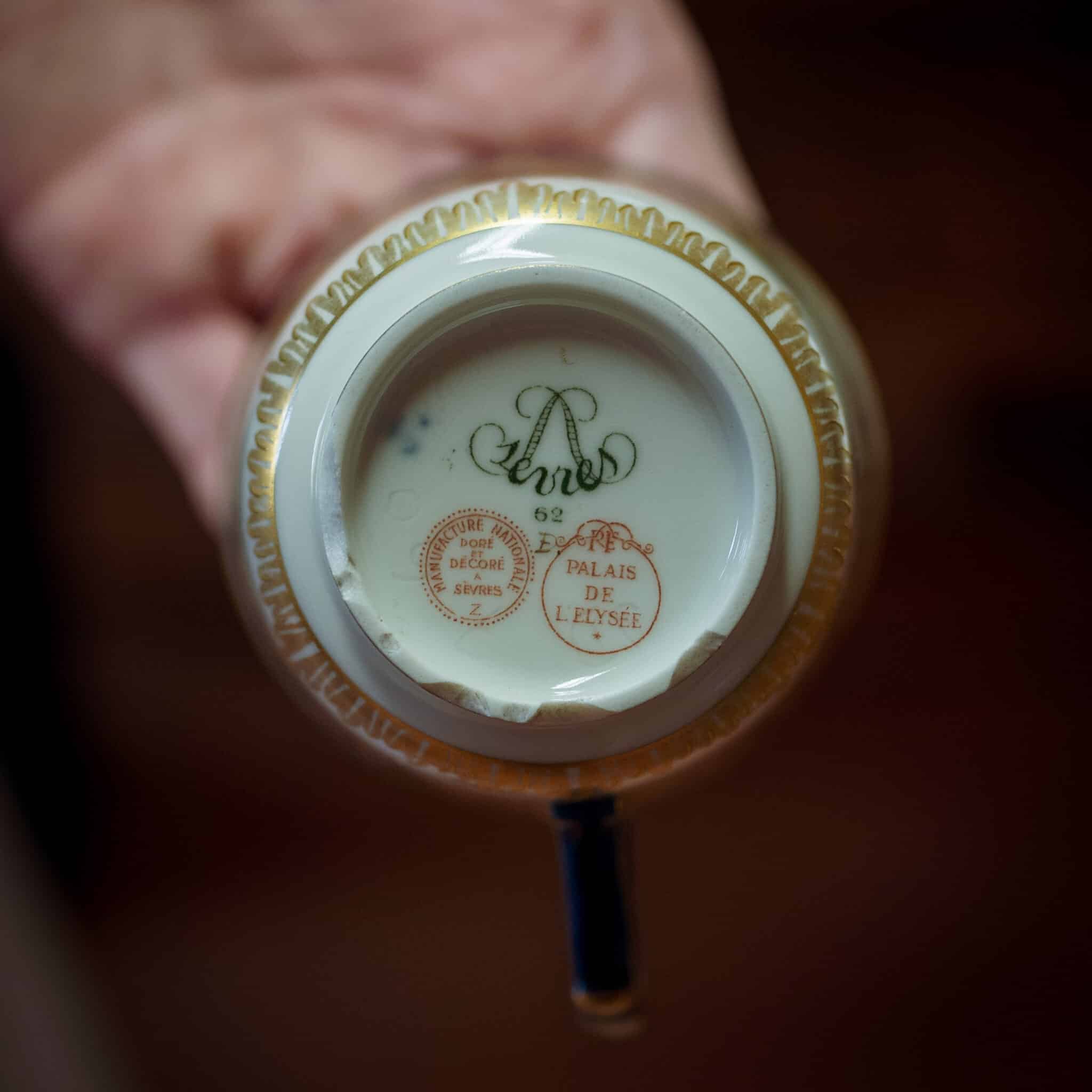
All of Sèvre’s agents are art technicians. As you talk with the artisans, you realize that each piece has an anecdote, a story to tell. And if these same artisans will confide in you with great modesty that they are not the artists and that they “only” produce the piece that has been asked of them, do not trust their testimony because their know-how requires long experience and high technicality. Without them, Sèvres would not exist.
Sèvres and contemporary art
Since the 18th century, the Sèvres Manufactory has been in the habit of collaborating with artists. A tradition that continues today and allows this old lady to keep her youthfulness and to push the technical limits of porcelain ever further.
Arman, Louise Bourgeois, Jean Arp, Johan Creten, Giuseppe Penone, Pierre Soulages, Lee Ufan, Zao Wou-ki, Annette Messager and many others have left their mark on the history of Sèvres and prove that porcelain remains resolutely modern.
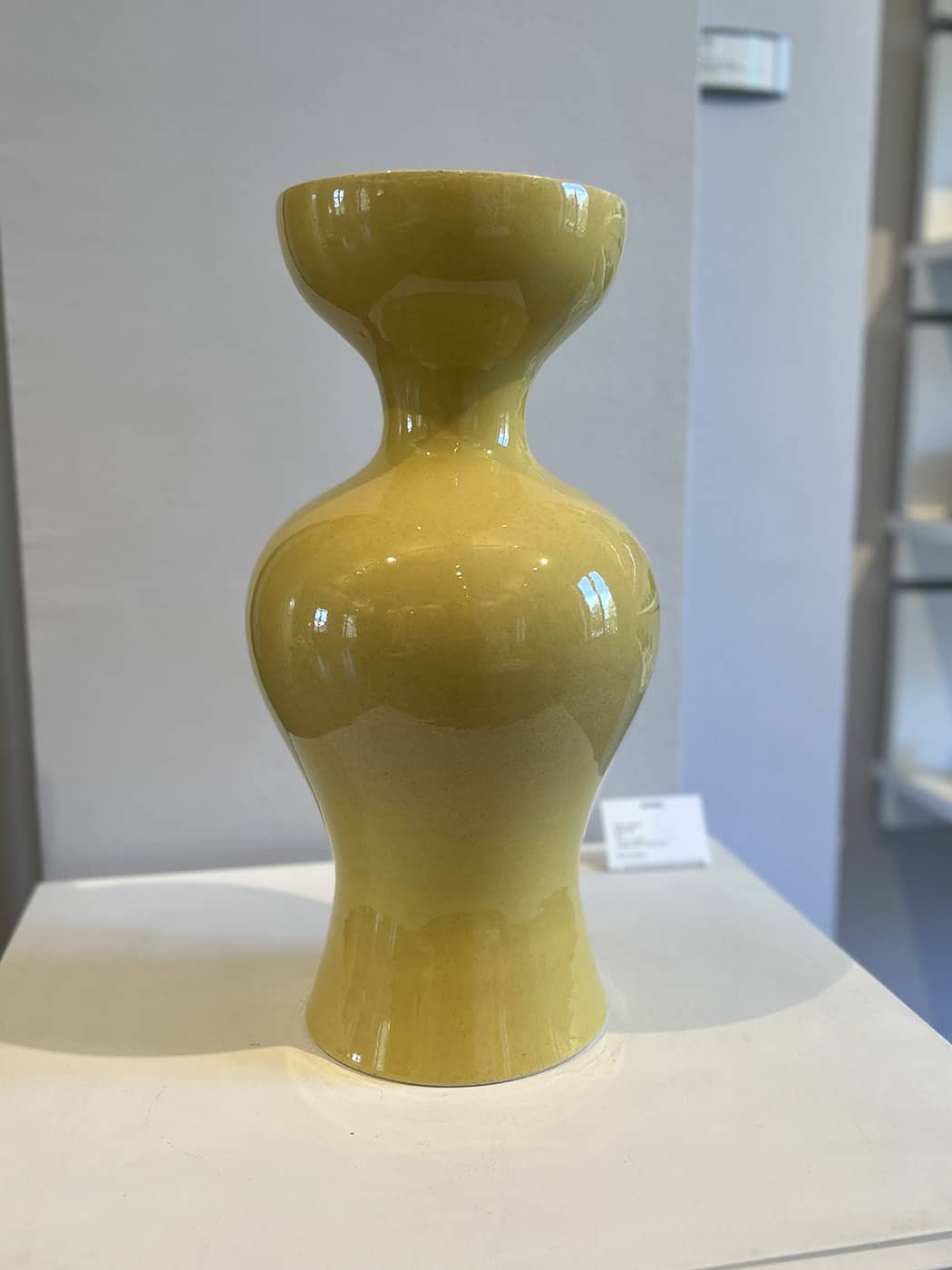

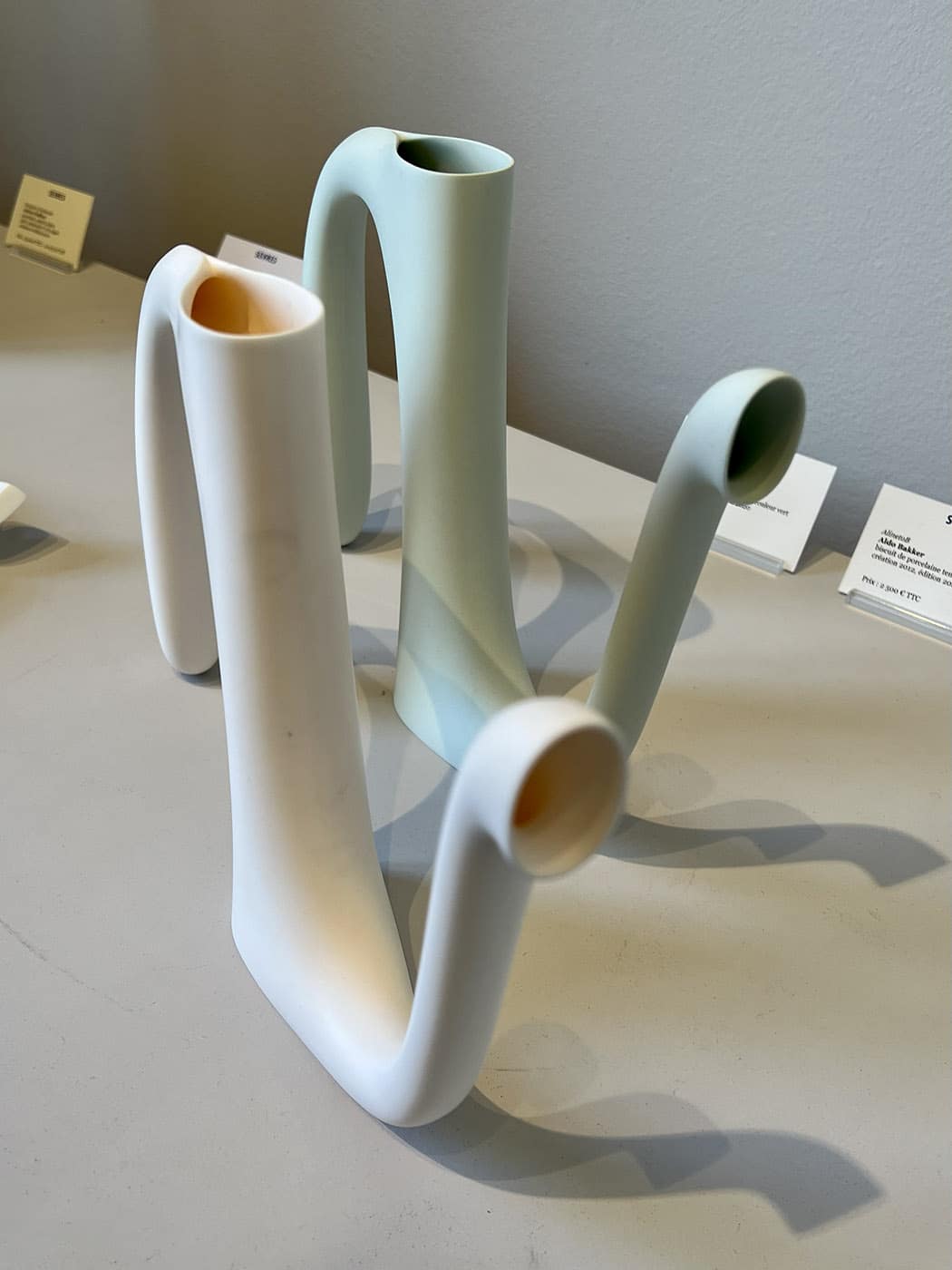
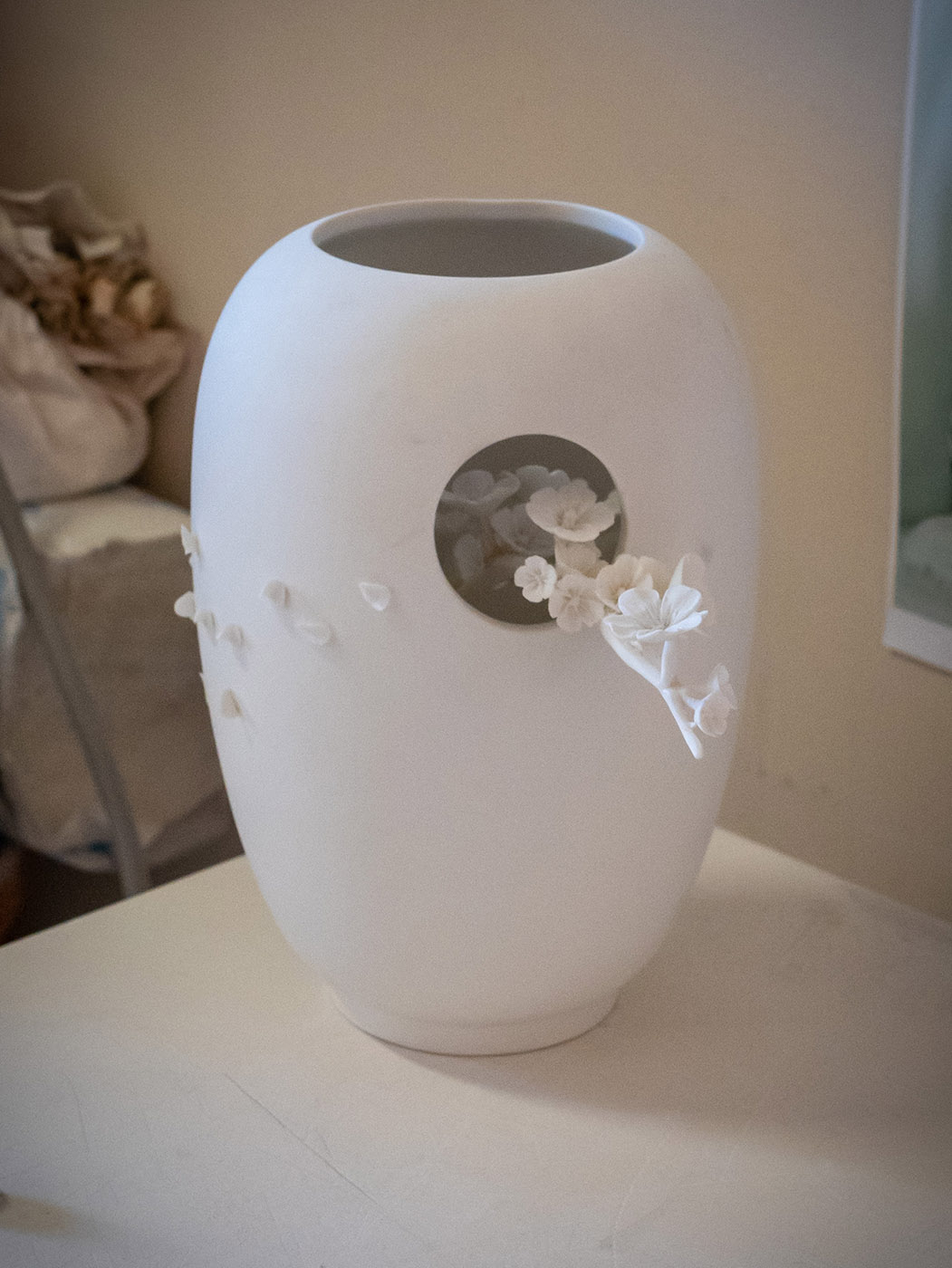
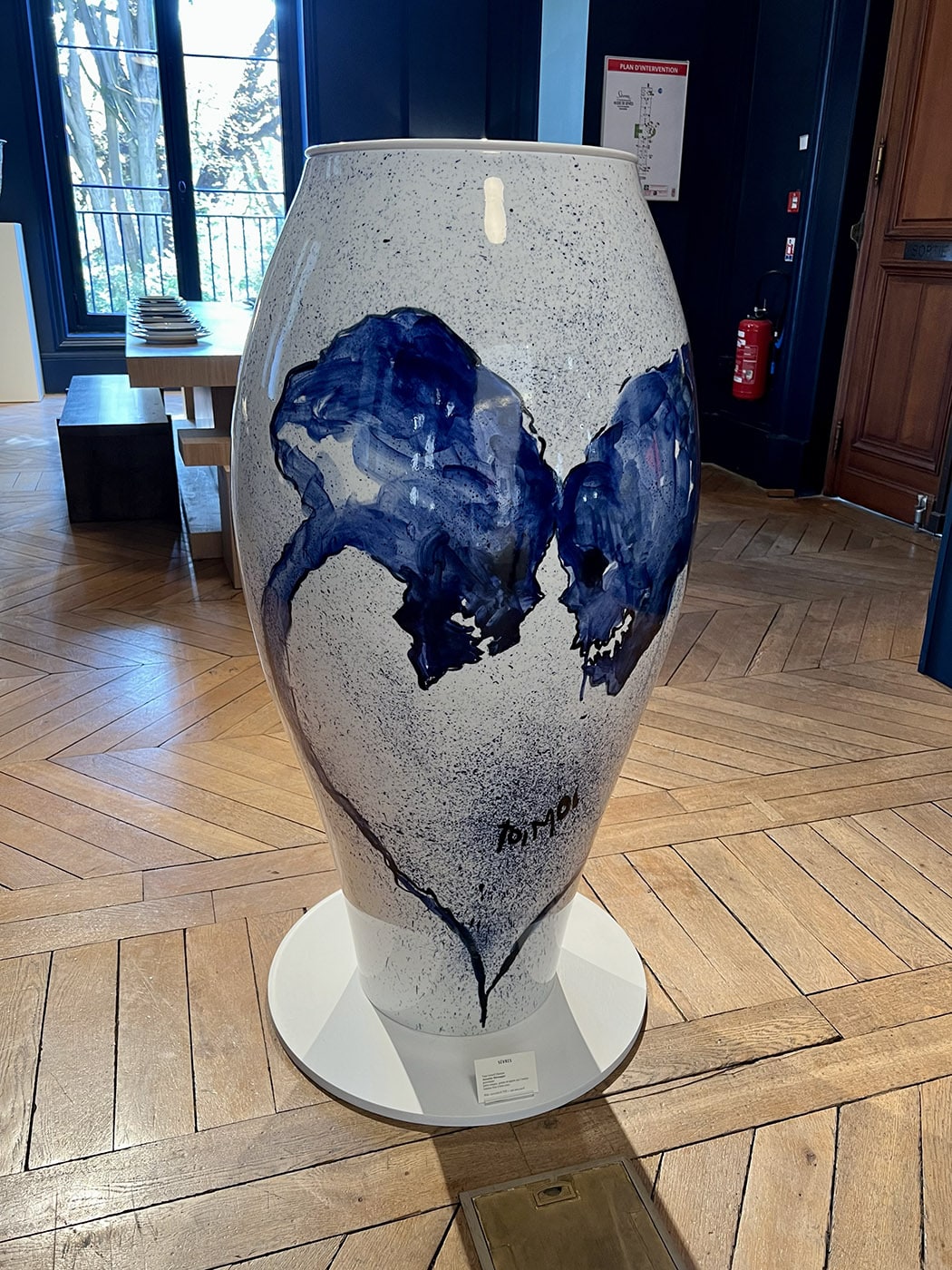
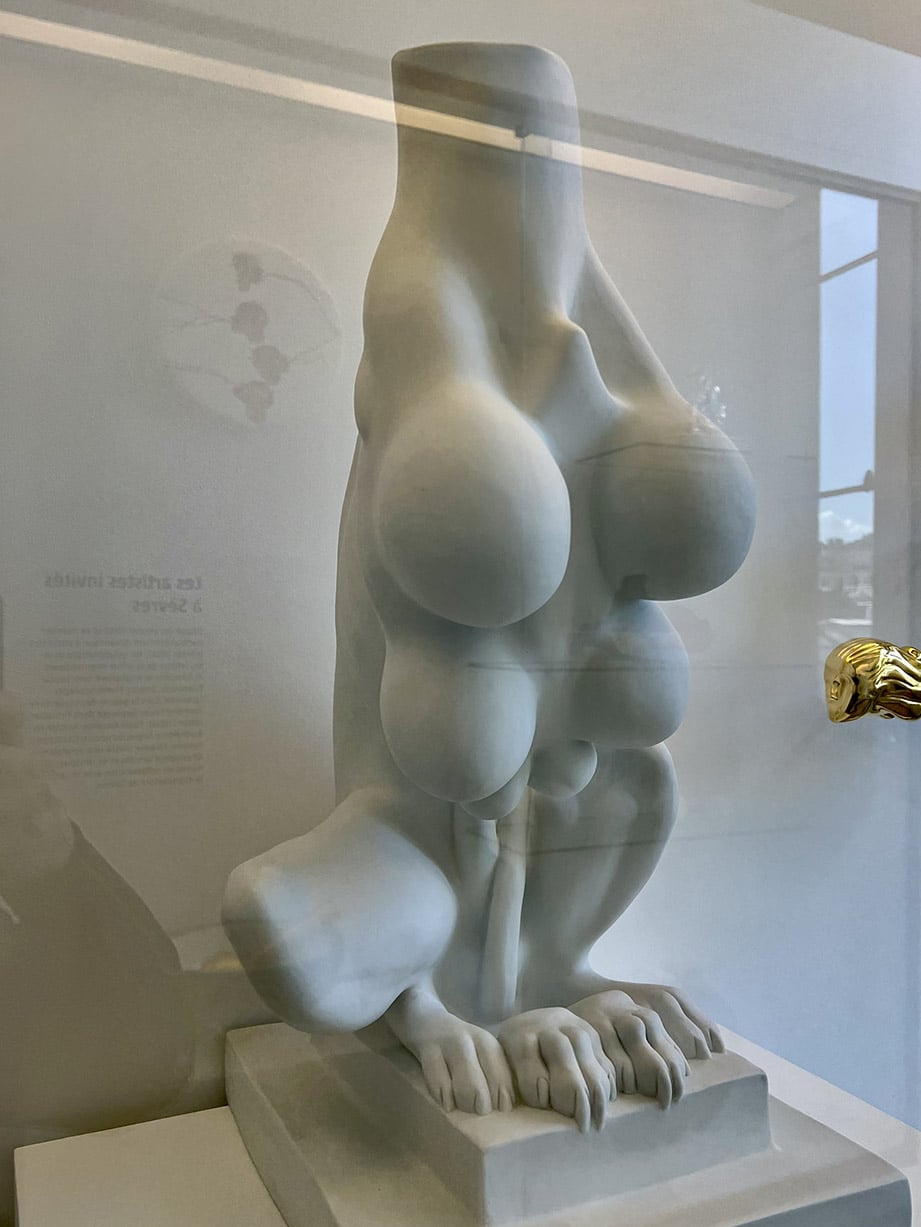
Birth of a Ceramics Museum
In 1800, Alexandre Brongniart was appointed to head the factory. For 47 years, this scientist will considerably develop Sèvres and give it an international reputation. He also initiated the creation of the museum, at a time when it was necessary to bring to Sèvres a center of ideas.
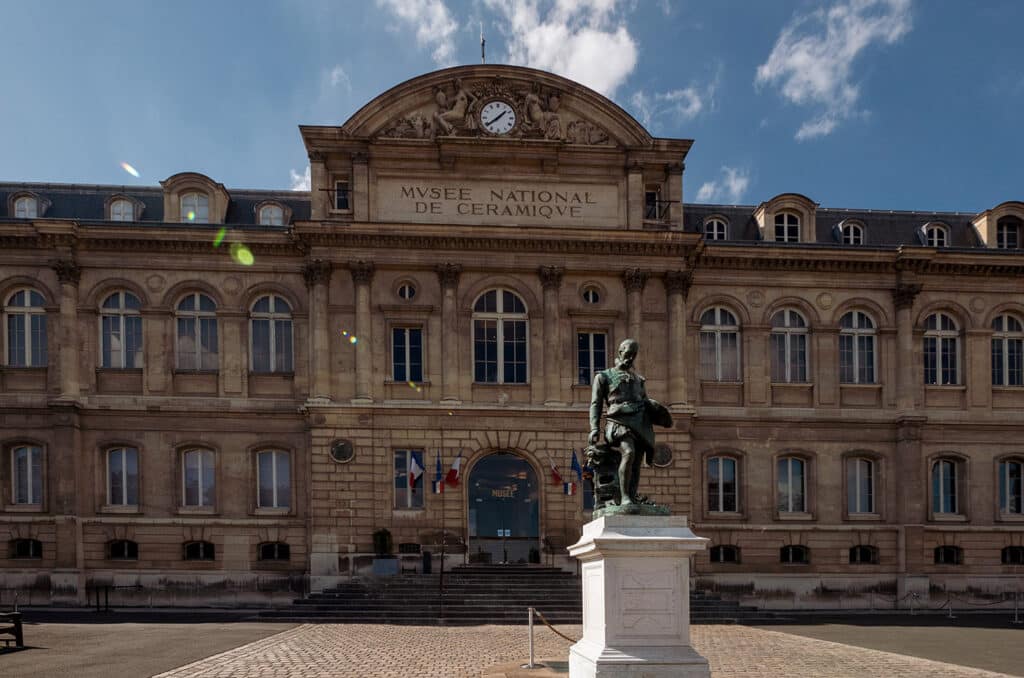
This museum with its international and universal vocation is not only dedicated to Sèvres. It is a museum of inspiration that has brought together forms, decorations, colors and techniques from all over the world, from antiquity to the present day. There are now more than 50,000 pieces, including several contemporary works.
“Porcelain is not just cups and saucers!”
Charlotte Vignon, Director of Heritage and Collections at the museum
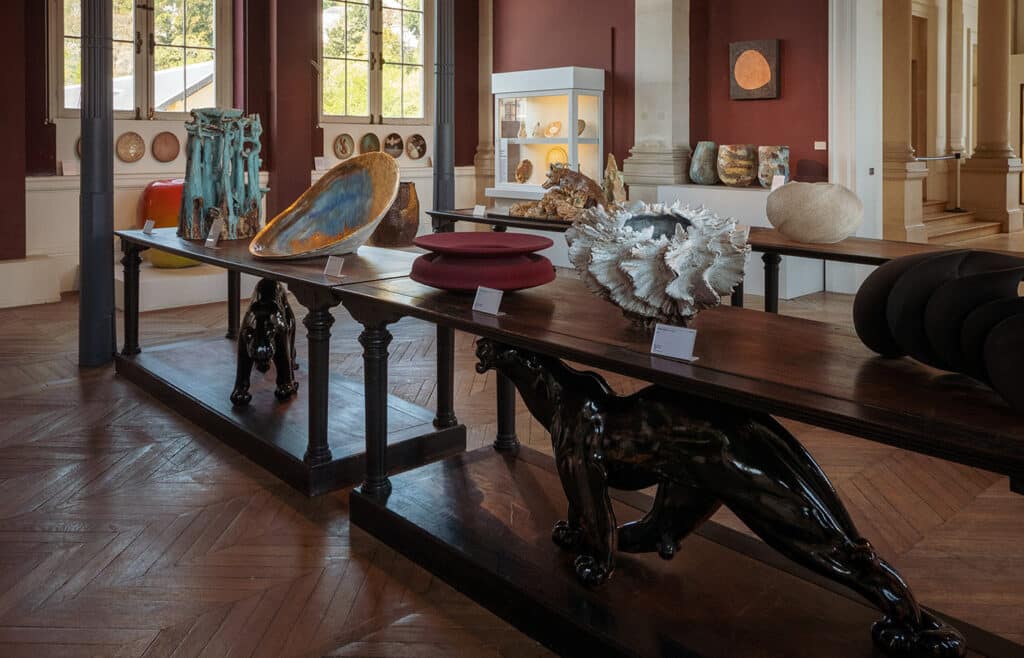
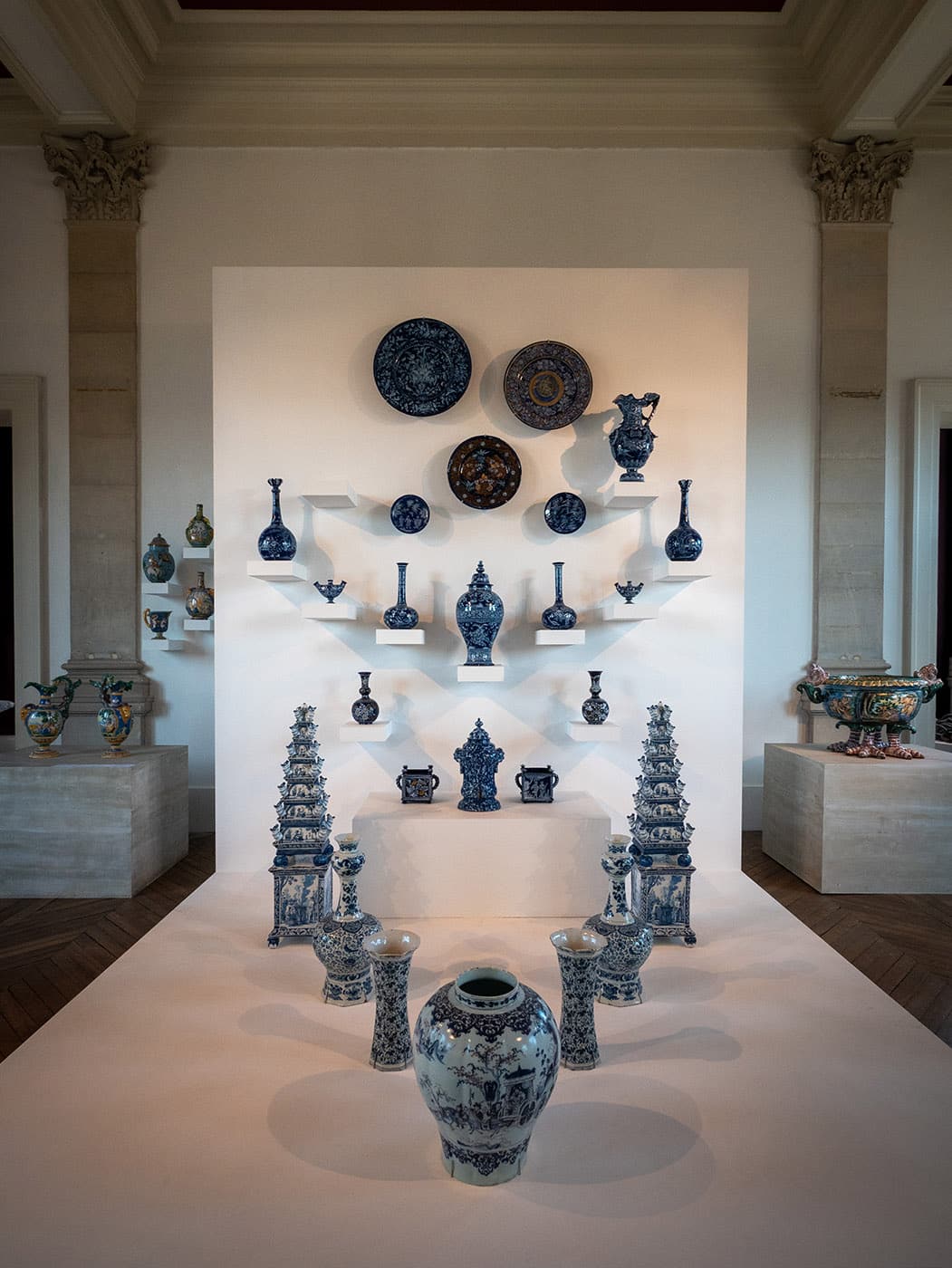
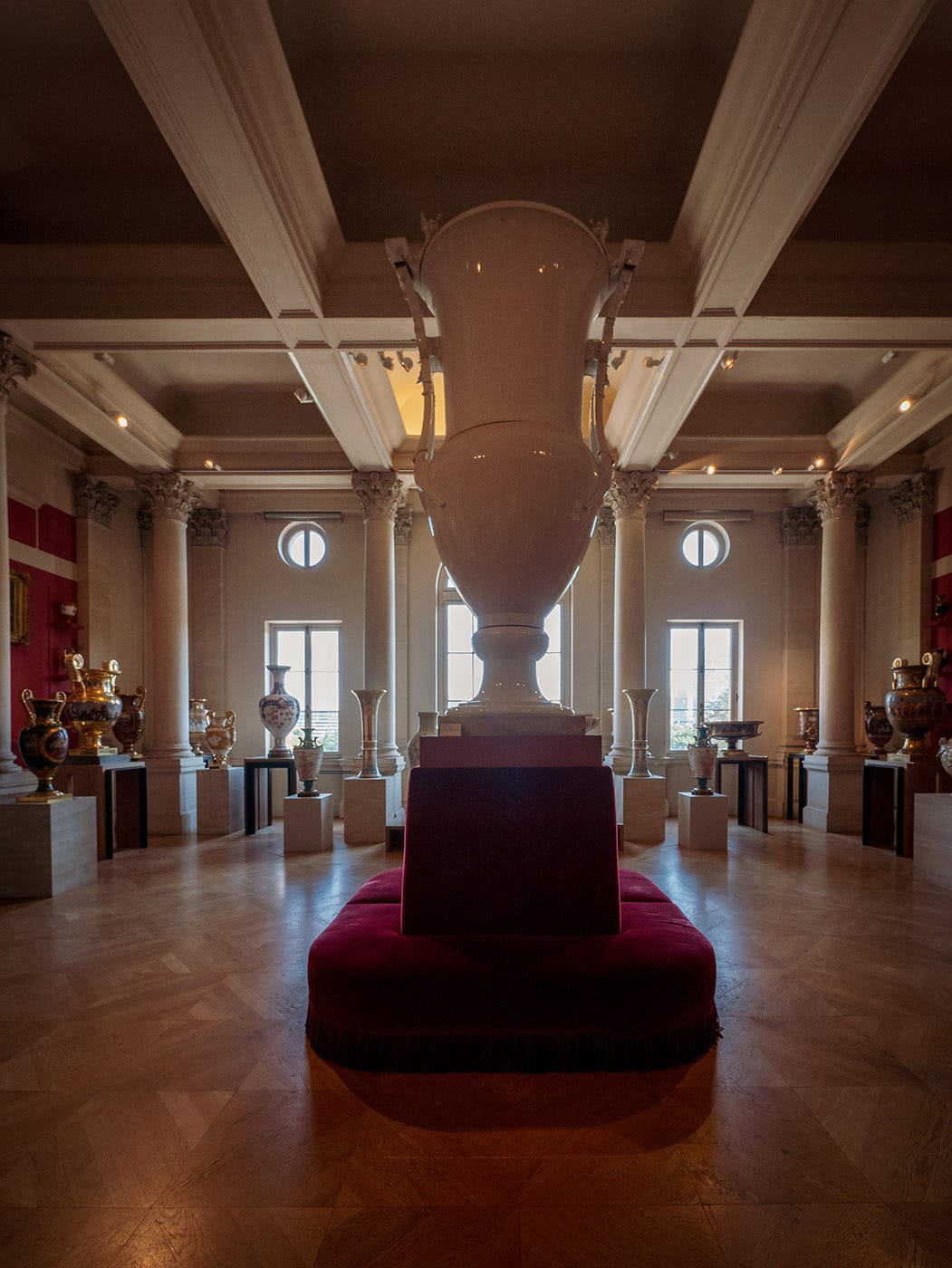
Buy a Sèvres porcelain
The factory produces mainly for the State and supplies in particular the table service of the Elysée. But some pieces are for sale, especially those related to contemporary creation.
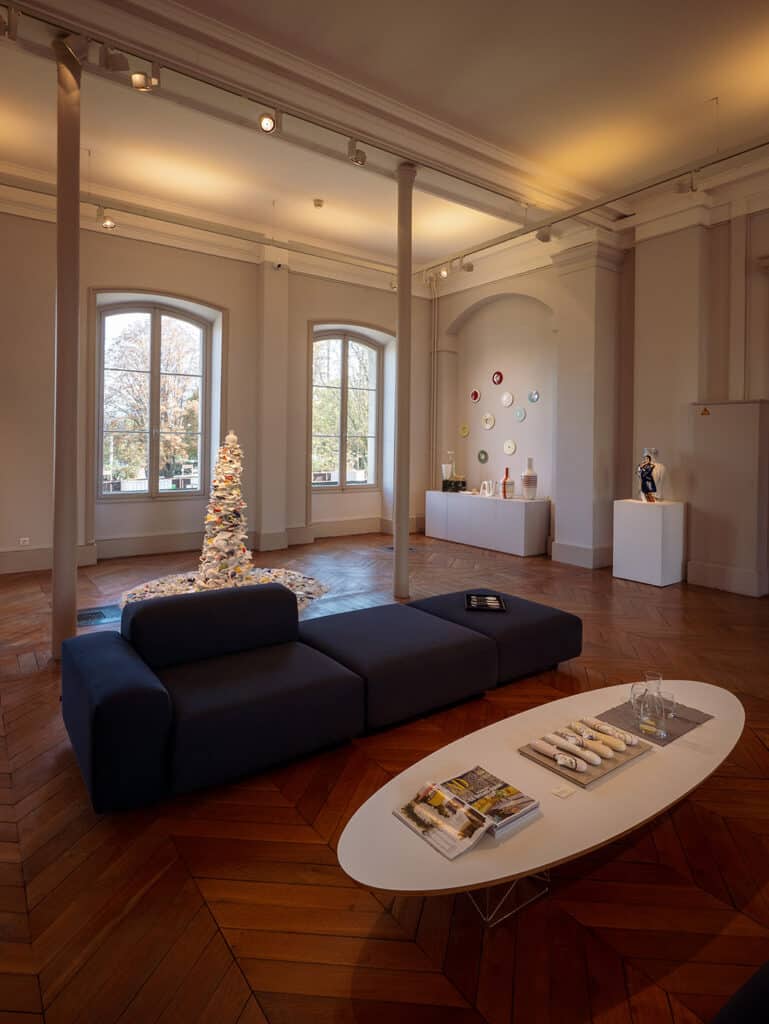
Of course, this handcrafted work has a cost, not everyone can afford a Sèvres service (count €600 for a cup!) and the most delicate pieces signed by renowned artists can largely exceed €100,000.
Some old porcelain regularly resurfaces in auction houses. Recently, three remarkable 19th century plates were sold at Auctie’s for between €9 and €19,000 each!
However, it is possible to make a (nice) gift by offering a small sculpture in Sèvres cookie (the porcelain left bare, without enamel or painted decoration), a jewel or a vase on the e-shop of the Manufacture. The first pieces are offered from 270 €.
As you can see, buying a piece produced at Sèvres is above all buying a know-how and a history, and that is priceless!
Useful informations
Please note that only the museum can be visited. The factory is only open to the public on rare occasions such as the Heritage Days.
Adress:
Sèvres – Ceramics museum
2 place de la Manufacture Nationale
92310 Sèvres (France)
Opening hours:
Every day except Tuesday
From 10am to 1pm and from 2pm to 6pm
Website:
https://www.sevresciteceramique.fr/en.html
Price:
Full price: €7.
Reduced rate : €5 for the exhibition
+€1 for temporary exhibitions
Free for children under 26 years old
Thanks to the Sèvres team and the craftsmen for their welcome and their explanations.
No Comments
Leave a comment Cancel